CNC Machining changed how we make things today. It lets machines create detailed parts on their own, with great accuracy. The system works through computer software that controls every move. In this piece, we’ll go over four key CNC Machining methods: Milling, Turning, Routing, and Grinding. These are used in many industries, from planes to phones, and each has its strengths.
What is CNC Machining?
CNC Machining means using computers to control machines that cut, drill, or shape materials. First, someone makes a digital design using CAD software. Then, the computer changes it into G-code, which tells the machine exactly what to do.
How CNC machines work:
Programming: First, the design is created and loaded into the CAD/CAM software for CNC machining.
Tool selection: Next, the appropriate tool is selected based on the material and job requirements.
Machining: The CNC machine then follows the program to perform tasks such as cutting, drilling, or grinding.
Finishing: Finally, the part undergoes final steps such as cleaning or coating to complete the entire machining process.
Advantages of CNC machining:
High precision: CNC machining can achieve very tight tolerances and can produce complex shapes that are difficult to achieve by hand.
Repeatability: Once programmed, CNC machining produces consistent parts every time, ensuring consistent quality.
High Efficiency: CNC machining is faster than manual methods and reduces human error.
Applications of CNC machining:
Automotive: CNC Machining is used to make precise engine components, transmission parts, and chassis parts, helping improve performance and safety.
Aerospace: CNC Machining produces high-precision turbine blades, structural frames, and landing gear that meet strict industry standards.
Electronics:It is used to create detailed parts like enclosures, connectors, and heat sinks, which are essential for electronic device function and protection.
Medical Devices: CNC Machining helps make surgical tools and implants with exact specifications to ensure safety and compatibility with the human body.
CNC Milling Service: Precision in Every Cut
CNC Milling is a type of CNC Machining that uses rotary cutters to remove material from a solid block. It creates features like holes, slots, and complex surfaces with high accuracy.
How CNC Milling Works:
Vertical Milling: The spindle is positioned vertically. It’s good for precision drilling, boring, and surface milling.
Horizontal Milling: The spindle lies flat. This setup works well for cutting large parts or doing heavy material removal.
Common CNC Milling Materials:
Metals: Materials such as aluminum, steel, and titanium are widely used because they are strong and easy to process.
Plastics: Materials such as acrylic, PVC, and ABS are lightweight and easy to shape.
Composites: Carbon fiber and fiberglass are strong and lightweight, making them suitable for making specialized parts.
Industries Benefiting from CNC Milling:
Aerospace: CNC Milling helps make complex parts for aircraft, such as airframe components.
Automotive: It’s used to machine engine blocks, transmission cases, and other key parts.
Medical: Precision milling is essential for making tools and implants that need to meet strict standards.
Advantages and disadvantages of CNC milling:
Pros: Offers high precision, works with many materials, and can shape complex designs.
Cons: Has higher setup costs, and tools may wear out over time, especially with hard materials.
CNC Turning: High-Speed Rotational Machining
CNC Turning is a type of CNC Machining where a spinning workpiece is shaped using a stationary cutting tool. It is mainly used to produce round or cylindrical parts with high speed and accuracy.
How CNC Turning Differs from Milling:
CNC Turning: The workpiece spins while the cutting tool stays in place.
CNC Milling: The cutting tool spins, and the workpiece stays still.
Turning shapes the outside of rotating parts, while milling works best for flat or complex surfaces.
Role of Lathes in CNC Turning:
CNC Lathes: These machines hold and rotate the material while the cutting tool removes unwanted sections.
Live Tooling: This feature allows the lathe to do extra tasks like drilling or light milling without moving the part to another machine.
Ideal Shapes and Parts Produced:
Cylindrical Components: Common examples include shafts, bushings, and pulleys.
Symmetrical Parts: Turning is perfect for items like bolts, nuts, and gears that need even, circular shapes.
Common Materials and Industries:
Materials: Metals like steel, aluminum, and brass are widely used because they are strong and easy to machine.
Industries: CNC Turning is important in automotive, aerospace, and medical device manufacturing, where round parts are needed.
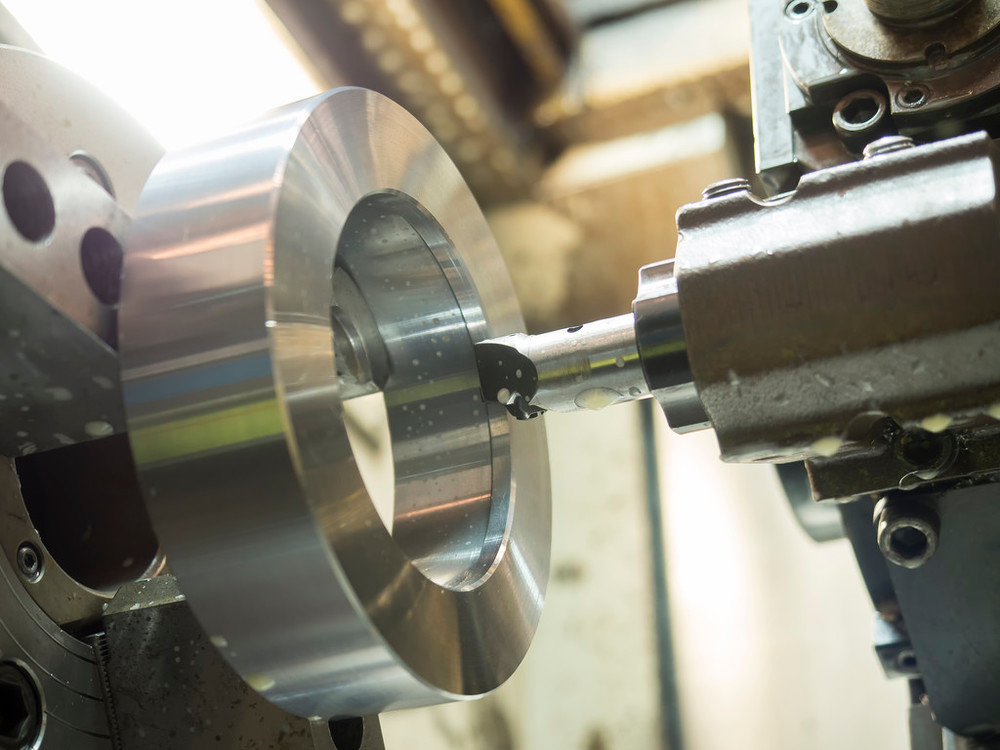
Advantages of Mass Production:
Speed: CNC Turning machines can produce parts quickly due to the continuous rotation of the workpiece.
Efficiency: It requires fewer tool changes and setup steps, which saves time during high-volume production.
CNC Routing: Precision for Wood, Plastic, and Soft Metals
CNC Routing is a type of CNC Machining that uses a spinning tool to cut, carve, or engrave materials like wood, plastic, and soft metals. It is ideal for projects that require detailed shapes and fast turnaround.
Unique Features of CNC Routing:
Design Flexibility: It can create detailed patterns, curves, and custom shapes with high precision.
Material Versatility: Works with many types of materials, even those with different sizes and thicknesses.
Difference Between CNC Routers and Mills:
CNC Routers: These are lighter machines made for softer materials like wood or plastic.
CNC Mills: Heavier machines that are better suited for cutting hard metals with tight tolerances.
Materials Best Suited for CNC Routing:
- Wood-Based: Common choices include hardwoods, plywood, and MDF.
- Plastics: CNC Routing works well with acrylic, PVC, and ABS.
- Soft Metals: Materials like aluminum and brass can also be routed with proper settings.
Common Uses:
- Sign Making: Ideal for cutting letters, logos, and custom signs with fine detail.
- Cabinetry: Used to produce furniture parts and decorative panels with clean edges.
- Prototyping: Useful for making design models quickly and accurately.
Advantages of CNC Routing:
- Cost-Effective: Lower setup costs compared to milling or turning, especially for soft materials.
- Rapid Prototyping: Fast production of design samples and custom parts, helpful for early testing.
CNC Grinding: Finishing with High Accuracy
What is CNC Grinding and When is it Used?
CNC Grinding is a part of CNC Machining that uses a spinning abrasive wheel to remove small amounts of material. It’s used when parts need very tight tolerances and smooth surface finishes. This makes it important for aerospace, medical, and high-performance automotive components.
CNC grinding helps shape parts with high precision and fine finishes. It’s ideal when surface quality and exact dimensions matter—like in turbine blades, medical implants, or high-speed engine parts.
Types of CNC Grinding Machines
- Surface Grinding: Uses a flat wheel to smooth the surface of flat parts.
- Cylindrical Grinding: Shapes the outside of round parts such as shafts or spindles.
- Centerless Grinding: Supports the part between wheels, allowing fast, continuous grinding without holding it in place.
- Internal Grinding: Used to finish inside holes or bores to precise dimensions.
Role in Producing Tight Tolerances and Surface Finishes
CNC grinding machines can reach tolerances as tight as ±0.0001 inches (±2.5 microns) and surface finishes as fine as Ra 0.2 micrometers. These capabilities are critical for high-performance parts that need to fit or move perfectly.
Materials Processed Through Grinding
CNC Grinding is highly versatile and can work with many materials:
- Metals: Steel, stainless steel, aluminum, titanium, brass, and copper.
- Hard Metals and Alloys: Tungsten carbide, Inconel, and superalloys.
- Ceramics: Alumina, silicon carbide, and zirconia.
- Composites: Carbon fiber reinforced polymers (CFRP) and glass fiber reinforced polymers (GFRP).
- Plastics: Engineering plastics and high-performance polymers.
- Glass and Optical Materials: Optical glass, quartz, and fused silica.
Applications in High-Precision Industries
CNC grinding plays a pivotal role in various high-precision industries:
- Aerospace: Manufacturing turbine blades, landing gear components, and control valves.
- Medical Devices: Producing surgical instruments, dental tools, and orthopedic implants.
- Tool Making: Sharpening and reconditioning cutting tools such as drills, end mills, and inserts.
- Automotive: Finishing engine components, transmission parts, and brake components.
Final ThoughtsComparing CNC Milling, Turning, Routing, and Grinding:
Process | Function | Ideal Materials | Surface Finish | Speed & Efficiency | Applications |
CNC Milling | Material removal via rotating cutter | Metals, plastics, and composites | Smooth to rough | Moderate | Aerospace, automotive, and medical devices |
CNC Turning | Rotating the workpiece with a stationary tool | Metals like steel, aluminum | Smooth to rough | High | Shafts, bushings, pulleys |
CNC Routing | High-speed cutting of materials | Wood, plastics, soft metals | Smooth | High | Signage, cabinetry, prototyping |
CNC Grinding | Abrasive finishing for precision | Metals, ceramics, and composites | Ultra-fine | Moderate | Aerospace, medical, and tool-making |
How to Choose the Right Process Based on Project Needs:
- Complex Part Geometry: CNC Milling or Routing offers the flexibility to produce detailed contours and multi-surface features.
- Rotational Parts: CNC Turning provides efficient and accurate production for cylindrical shapes.
- Tight Tolerance Requirements: CNC Grinding delivers superior precision and fine surface finishes.
Non-Metal Materials: CNC Routing is optimized:
CNC Machining includes a variety of processes, each offering unique benefits for specific manufacturing needs. Selecting the right process based on function, material, and design requirements leads to better quality control, improved efficiency, and stronger end products.
Frequently Asked Questions:
Q1: Turning vs. Milling—what’s the difference?
CNC turning spins the workpiece while the cutting tool stays still—great for round or cylindrical parts. CNC milling, on the other hand, uses a rotating tool to shape a fixed workpiece, perfect for flat surfaces and complex contours.
Q2: Can routers cut metal?
Sort of. Routers can handle soft metals like aluminum, but for steel or harder materials, go with milling or turning.
Q3: How accurate is grinding?
Super accurate. CNC grinding is one of the most precise CNC Machining processes. It can reach tolerances of ±0.0001 inches and surface finishes as fine as Ra 0.2 microns.
Q4: Can one CNC machine do everything?
Some machines can! Some multi-function CNC machines can handle milling, turning, and even grinding in one setup, which helps save time and improve workflow.