Sheet Metal Plasma Cutting Service
Our Custom Sheet Metal Plasma Cutting Services
NOBLE’s custom sheet metal plasma cutting services provide fast, precise, and cost-effective solutions for cutting a wide range of metals. Using advanced sheet metal cutting technology, we specialize in creating complex, high-quality sheet metal plasma cut parts quickly with minimal waste.
- 10+ Years of Sheet Metal Plasma Cutting
- Advanced Equipment & Competitive Price
- ISO 9001 & ISO13485 Certified Factory
- Guaranteed Consistent Quality
- 100% Part Inspection
- 99.5% On-time Delivery
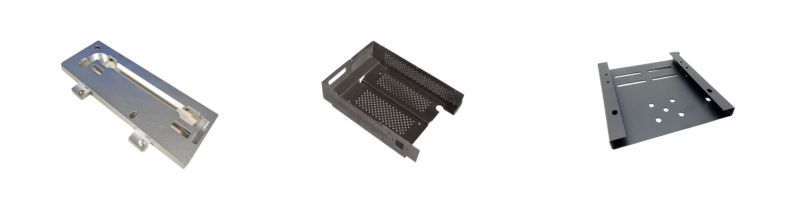
STEP | STP | STL | IGS | IGES | PRT | SLDPRT | SAT | X_T | IPT | CATPART | PDF
Max. file size: ≤20MB
- All uploads are secure and confidential.
Our Powerful Sheet Metal Cutting Processes
At NOBLE, we offer a comprehensive range of precision sheet metal cutting services using a range of techniques. Each method is suitable for specific materials, thicknesses, and accuracy requirements. Depending on your needs, we will help you choose the most sheet metal cutting appropriate one.
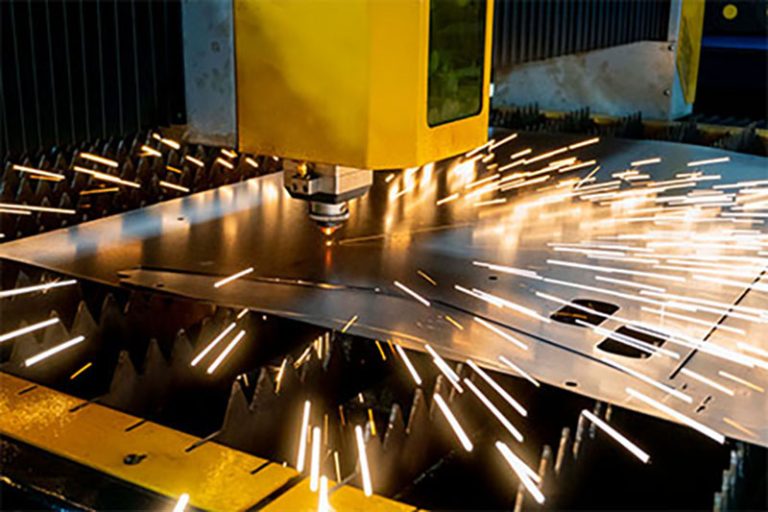
Sheet Metal Laser Cutting is a high-precision method that uses a focused laser beam to cut or engrave materials. The laser beam melts, burns, or vaporizes the material, resulting in a clean, precise cut.
- 10+ Years of Sheet Metal Laser Cutting
- 20,000+Customer Served
- 100% Inspection
- Quality Parts Made Easier, Faster
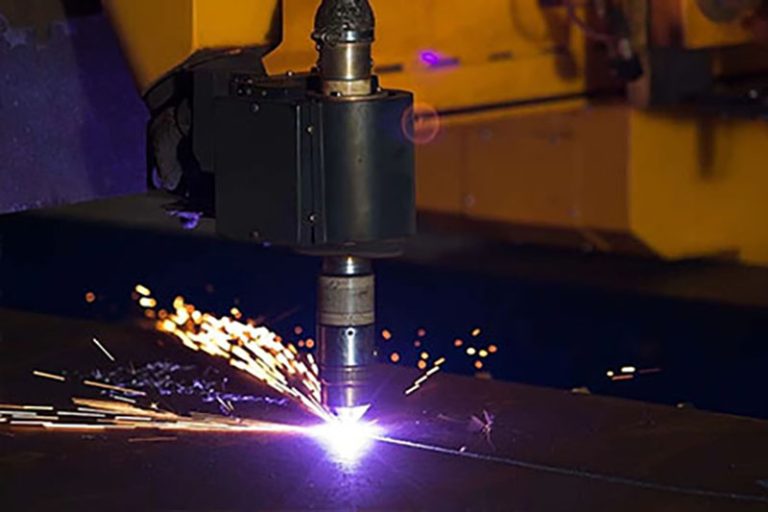
Sheet Metal Plasma cutting uses a high-temperature plasma arc to melt and blow away material, mainly for cutting conductive metals. Plasma cutting is highly effective for cutting thicker metals quickly.
- 10+ Years of Sheet Metal Plasma Cutting
- Fast Turn-around Production
- 99.5% On-time Delivery
- Quote Within 12 hours
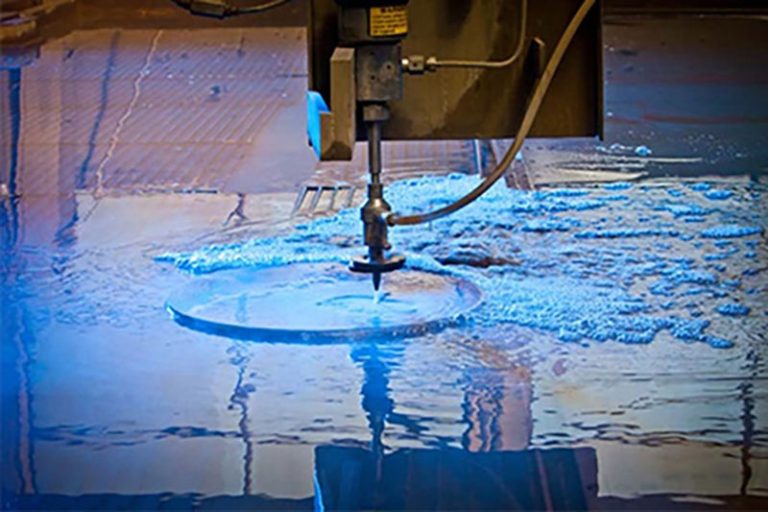
Sheet Metal Waterjet cutting uses a high-pressure stream of water, sometimes with abrasives, to cut through various materials. It’s a non-thermal process, meaning the material isn’t subjected to extreme heat, thus avoiding thermal distortion and changes in material properties.
- Advanced Equipment & Competitive Price
- Fast Turn-around production
- 99.5% On-time Delivery
- 10+ Years of Sheet Metal Waterjet cutting
Our Robust Sheet Metal Plasma Cutting Capabilities
Sheet Metal Prototyping to Production
NOBLE is your trusted one-stop custom manufacturing solution. From prototype design to production, we utilize extensive manufacturing resources, the right technology, streamlined processes, expert guidance, and a thorough quality inspection system to turn your ideas into reality.
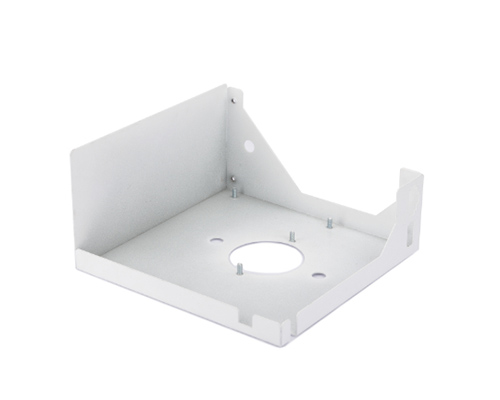
Sheet Metal Prototype Machining
Our sheet metal prototypes are produced within a few days at a low unit cost, thanks to advanced production equipment and an experienced engineering team. We ensure strict tolerance control and a comprehensive quality inspection process.
- State-of-the-art Equipment
- 10+ Years of Sheet Metal Manufacturing
- Competitive & Affordable Price
- Quote Within 24 hours
- Free DFM Feedback
- Fast Turnaround in 7 days
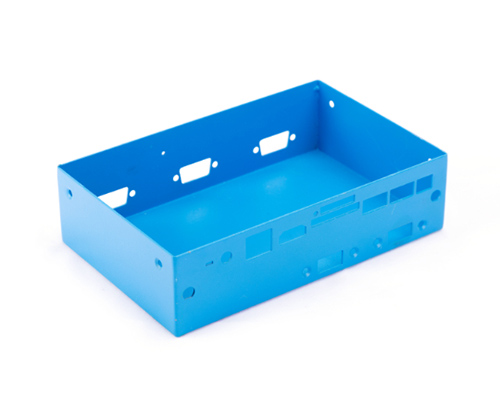
Rapid Sheet Metal Prototyping
Our sheet metal prototypes are produced within a few days at a low unit cost, thanks to advanced production equipment and an experienced engineering team. We ensure strict tolerance control and a comprehensive quality inspection process.
- Competitive & Affordable Price
- State-of-the-art Equipment
- 10+ Years of Low-Volume Manufacturing
- Fast Lead Time
- 30+ Countries Shipped
- 100% Part Inspection
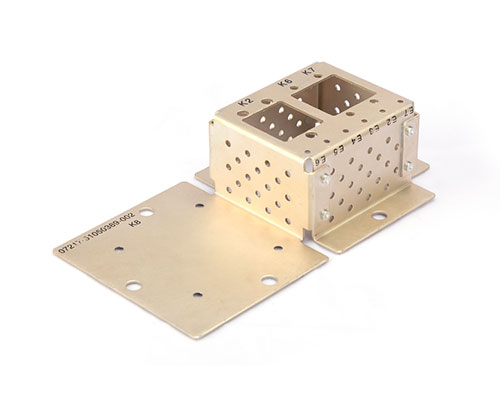
Batch Sheet Metal Production
NOBLE meets mass production demands with strict tolerance control, quality inspection, and a complete supply chain, ensuring the fast delivery of large quantities of low-cost, high-performance sheet metal parts.
- 10+ Years of Medium&Mass Production
- Competitive & Affordable Price
- Large Supplier Network
- 100,0000+ Unique parts produced
- Guaranteed Consistent Quality
- Fast Turn-Around Production
Why Choose Us for Custom Sheet Metal Plasma Cutting Service
NOBLE uses advanced technology and has a team of skilled professionals who are dedicated to putting our customers first. Our rapid tooling services are precise, efficient, cost-effective, and produce high-quality sheet metal plasma cutting production. By choosing our sheet metal plasma cutting services, you can elevate your business to new levels of success.
Expert Technicians
Our team consists of highly skilled technicians with extensive experience in sheet metal plasma-cutting technology. Their deep understanding of the process allows them to deliver parts that perfectly match your specifications, ensuring precision and efficiency at every step.
Specialized Customization
No matter the complexity of your project, we offer complete customization. From simple cuts to intricate designs, our team adapts to your specific needs and ensures that each part is fabricated to your exact requirements, delivering exceptional results every time.
Fast Turnaround
Thanks to the speed and precision of sheet metal plasma cutting, we can deliver your sheet metal plasma-cutting parts quickly, whether you’re looking for a prototype or a large production run. Our efficient process ensures you get high-quality parts without unnecessary delays.
Quality Assurance
We are committed to maintaining the highest standards of quality control. Every sheet metal plasma-cutting part undergoes rigorous inspection to ensure it meets the required specifications and durability standards, providing you with consistent, top-quality results on every
Work with Us in 4 Simple Steps Only
With many years of manufacturing experience, NOBLE offers the best solutions for all rapid prototyping and low-volume manufacturing needs. We streamline the innovation cycle into four simple but effective steps.



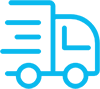
Sheet Metal Plasma Cutting Standards
To ensure part operability and precision for manufacturing prototypes and parts, our custom sheet metal laser cutting services comply with ISO 2768-m. To give you a clearer understanding, we provide sheet metal laser cutting tolerances for different parts for your reference.
Dimension Detail | Tolerance |
Edge to Edge, Single Surface | +/- 0.010″ |
Edge to Hole, Single Surface | +/- 0.010″ |
Hole to Hole, Single Surface | +/- 0.010″ |
Hole Diameter, Single Surface | +/- 0.010″ |
Bend to Edge / Hole, Single Surface | +/- 0.010″ |
Edge to Feature, Multiple Surface | +/- 0.030″ |
Over Formed Part, Multiple Surface | +/- 0.030″ |
Bend Angle | +/- 1 deg |
Materials for Custom Sheet Metal Plasma Cutting
Sheet Metal plasma cutting has a wide range of applications across various industries due to its precision, speed, and ability to cut through a variety of materials. Our state-of-the-art plasma cutting equipment can handle a wide range of materials and thicknesses, making us the go-to choice for all your custom cutting needs.
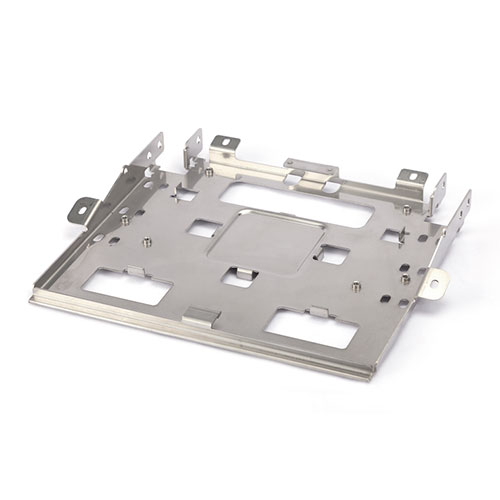
Stainless Steel
Stainless steel is widely used in industries like food processing, aerospace, and medical devices. It’s resistant to corrosion, and plasma cutting can make precise cuts, but speed and gas adjustments are needed to prevent oxidation.
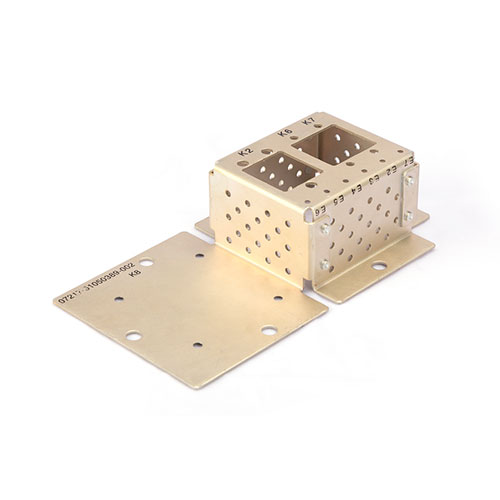
Brass
Brass, a copper-zinc alloy, is used in electrical and mechanical applications. Plasma cutting works well, but like copper, controlling heat and speed is important for maintaining quality cuts.
Wall Thickness: 0. 75 mm
Lead Time: 3 days
Tolerances: ±0. 01mm
Max part size: 200 x 80 x 100 cm
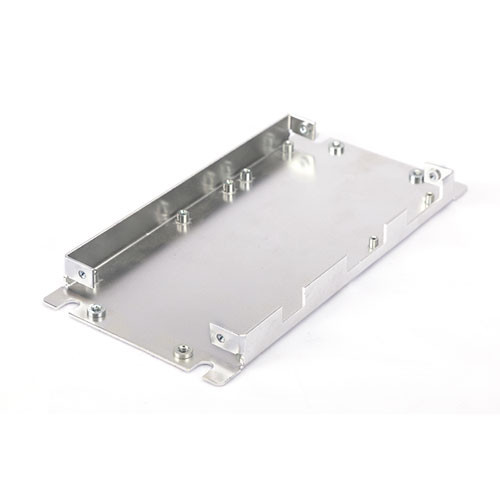
Aluminum
Aluminum is lightweight, corrosion-resistant, and ideal for aerospace, automotive, and marine uses. Plasma cutting can be challenging due to its low melting point and high thermal conductivity, but with the right adjustments, it produces clean cuts, especially in thin gauges.
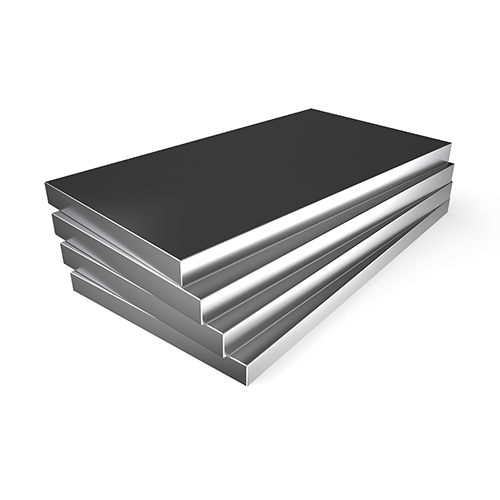
Titanium
Titanium is strong and lightweight, commonly used in aerospace and medical devices. Plasma cutting titanium needs careful control of temperature and gas mixture to prevent oxidation and ensure clean cuts.
Surface Finishes for Sheet Metal Plasma Cutting
Enhance durability and appeal with our various finishing options.Part surface finishing techniques can be used for either functional or aesthetic purposes. Each technique has specific requirements, such as materials, color, texture, and price. Improve the quality of your plasma-cutting parts today!
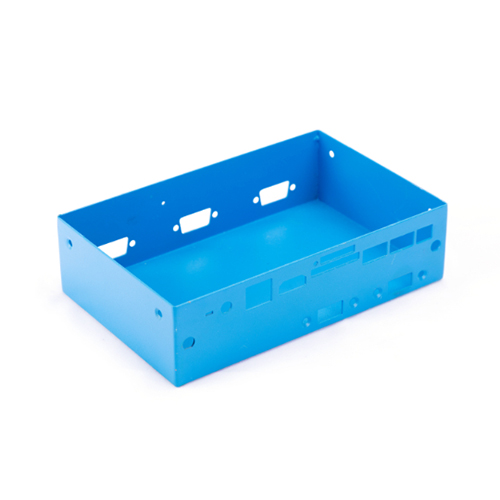
Anodizing
Anodizing improves corrosion resistance, enhancing wear resistance and hardness, and protecting the metal surface. Widely used in mechanical parts, aircraft, and automobile parts, precision instruments, etc.
Materials: Aluminum
Color: Clear, black, grey, red, blue, gold.
Texture: Smooth, matte finish
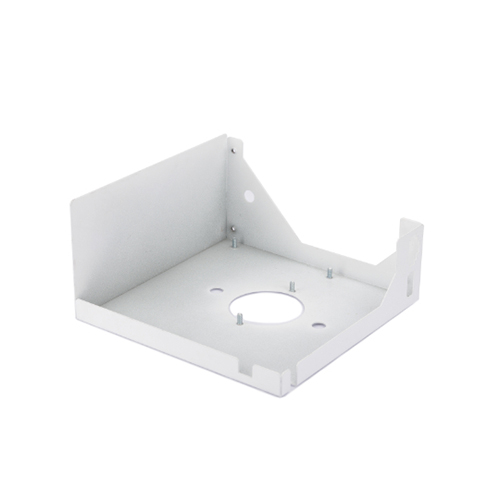
Sand Blasting
Sand blasting results in parts with a smooth surface with a matte texture. Used mainly for visual applications and can be followed by other surface treatments.
Materials: ABS, Aluminum, Brass
Color: N/A
Texture: Matte
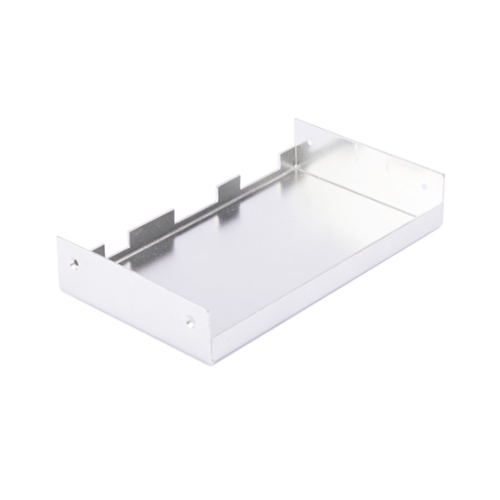
Powder Coating
Powder coating is a type of coating that is applied as a free-flowing, dry powder. Unlike conventional liquid paint which is delivered via an evaporating solvent, powder coating is typically applied electrostatically and then cured under heat or with ultraviolet light.
Materials: Aluminum, Stainless Steel, Steel
Color: Black, any RAL code or Pantone number
Texture: Gloss or semi-gloss
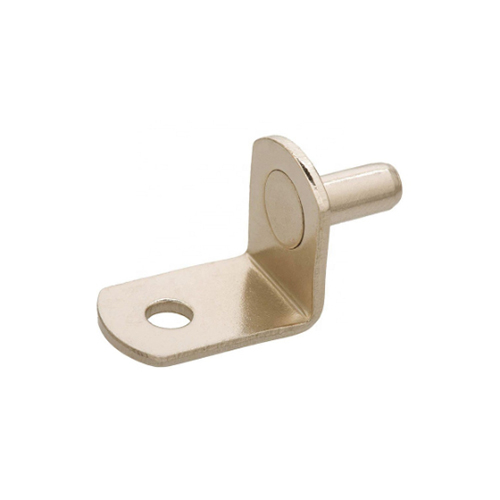
Electroplating
Electroplating can be functional, decorative or corrosion-related. Many industries use the process, including the automotive sector, in which chrome-plating of steel automobile parts is common.
Materials: Aluminum, steel, Stainless Steel
Color: N/A
Texture: Smooth, Glossy finish
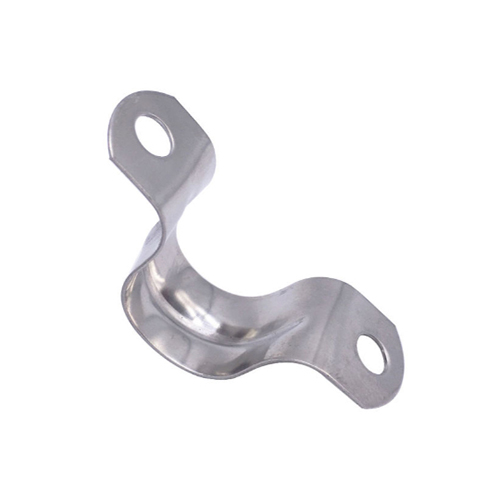
Polishing
Polishing is the process of creating a smooth and shiny surface, either through physical rubbing of the part or by chemical interference. The process produces a surface with significant specular reflection, but in some materials is able to reduce diffuse reflection.
Materials: Aluminum, Brass, Stainless Steel, Steel
Color: N/A
Texture: Glossy
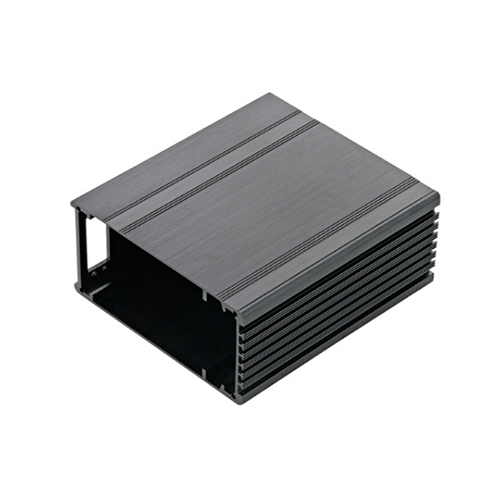
Brushing
Brushing is a surface treatment process in which abrasive belts are used to draw traces on the surface of a material, usually for aesthetic purposes.
Materials: ABS, Aluminum, Brass, Stainless Steel, Steel
Color: N/A
Texture: Satin
Custom Sheet Metal Plasma Cutting Parts Display
For more than ten years, NOBLE has been focusing on providing sheet metal plasma cutting services for different metal materials and prototypes. The following are sheet metal plasma cutting parts customized by NOBLE for customers.
See What Our Customers Say About Us
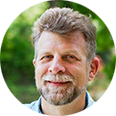
John Carter
Production Manager
We’ve worked with several cutting services over the years, but what sets NOBLE apart is the precision and consistency in their plasma cutting. We rely heavily on precise cuts for our automotive components, and we’ve never had an issue with quality. The results are always spot-on, and the parts fit perfectly without the need for secondary machining.
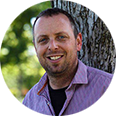
David Miller
CEO
We’ve been using this plasma cutting service for a few years, and the cost-effectiveness has been a game-changer for us. Not only do we save on material costs due to the precision cuts, but we also reduce our labor and operational expenses. NOBLE’s prices are very competitive, and the quality makes it worth every penny. We’re seeing a strong return on investment.
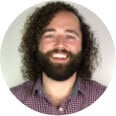
Olivia Thompson
Lead Engineer
One of the reasons we chose NOBLE is their ability to customize solutions. We needed specific cuts for custom steel brackets, and they took the time to understand our needs and provided exactly what we were looking for. Whether it’s adjusting to unique dimensions or working with unconventional materials, NOBLE’s team is flexible and always willing to adapt to our project requirements.
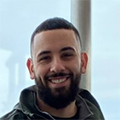
Michael Richard
Senior Fabricator
The cuts we get from NOBLE’s service are clean, with very little dross or oxidation. It has made our post-processing workflow so much easier—there’s almost no grinding or extra cleaning required. The quality of the edge finish allows us to save time and focus on other aspects of production. It’s rare to find such high-quality cuts in plasma cutting, and that’s why we keep coming back.
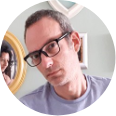
Rachel Lawson
Project Manager
The cuts we get from NOBLE’s service are clean, with very little dross or oxidation. It has made our post-processing workflow so much easier—there’s almost no grinding or extra cleaning required. The quality of the edge finish allows us to save time and focus on other aspects of production. It’s rare to find such high-quality cuts in plasma cutting, and that’s why we keep coming back.
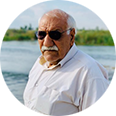
Ethan Walker
Purchasing Director
We work with a variety of materials in our production, from aluminum to stainless steel and brass, and NOBLE have consistently delivered excellent results across the board. We needed a cutting service that could handle everything without compromising quality, and NOBLE has consistently exceeded our expectations. No matter the material or thickness, the cuts are always precise.
Our Sheet Metal Plasma Cutting for Various Applications
As one of the leading precision machining suppliers in China, NOBLE has been providing rapid prototyping and precision quality machining services for more than 10 years. We have exported millions of plasma-cut parts around the world, helping many OEM customers in a wide range of industries turn their ideas into products and achieve good results.
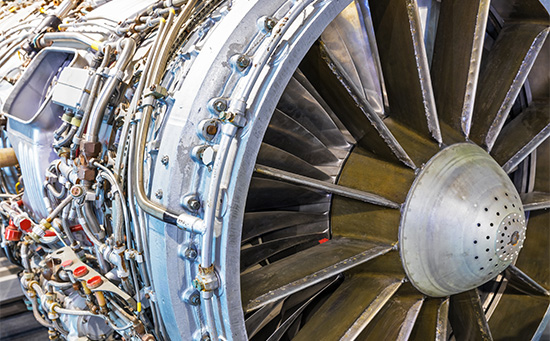
Aerospace Parts
Plasma cutting is used to make precise aerospace components, like fuselages and engine parts, from titanium and aluminum, offering high precision and minimal distortion for complex designs.
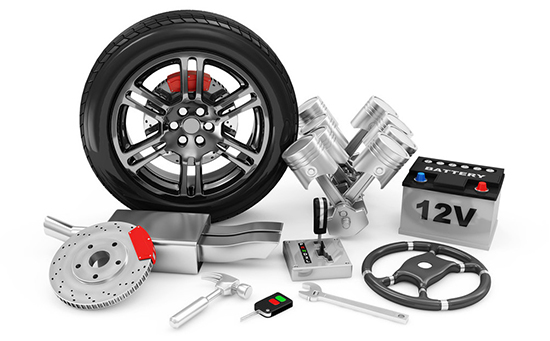
Automotive Parts
Plasma cutting efficiently cuts automotive parts like frames, brackets, and exhaust systems, providing fast, clean cuts, low waste, and cost-effective production for high-volume manufacturing.
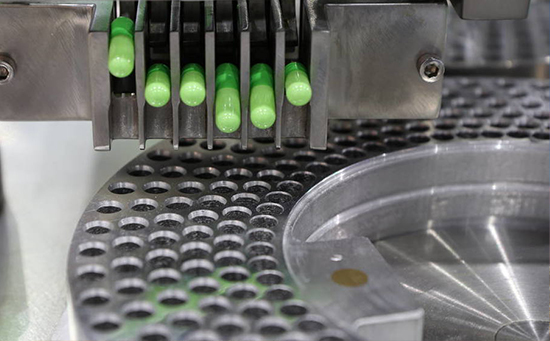
Medical Devices
Plasma cutting is used to make surgical instruments and implants, especially from stainless steel and titanium, ensuring high precision and durable, sterile components for medical use.

New Energy
Plasma cutting is used in renewable energy sectors like solar, wind, and battery storage to make durable components, such as solar panel frames and wind turbine parts, from aluminum and stainless steel.
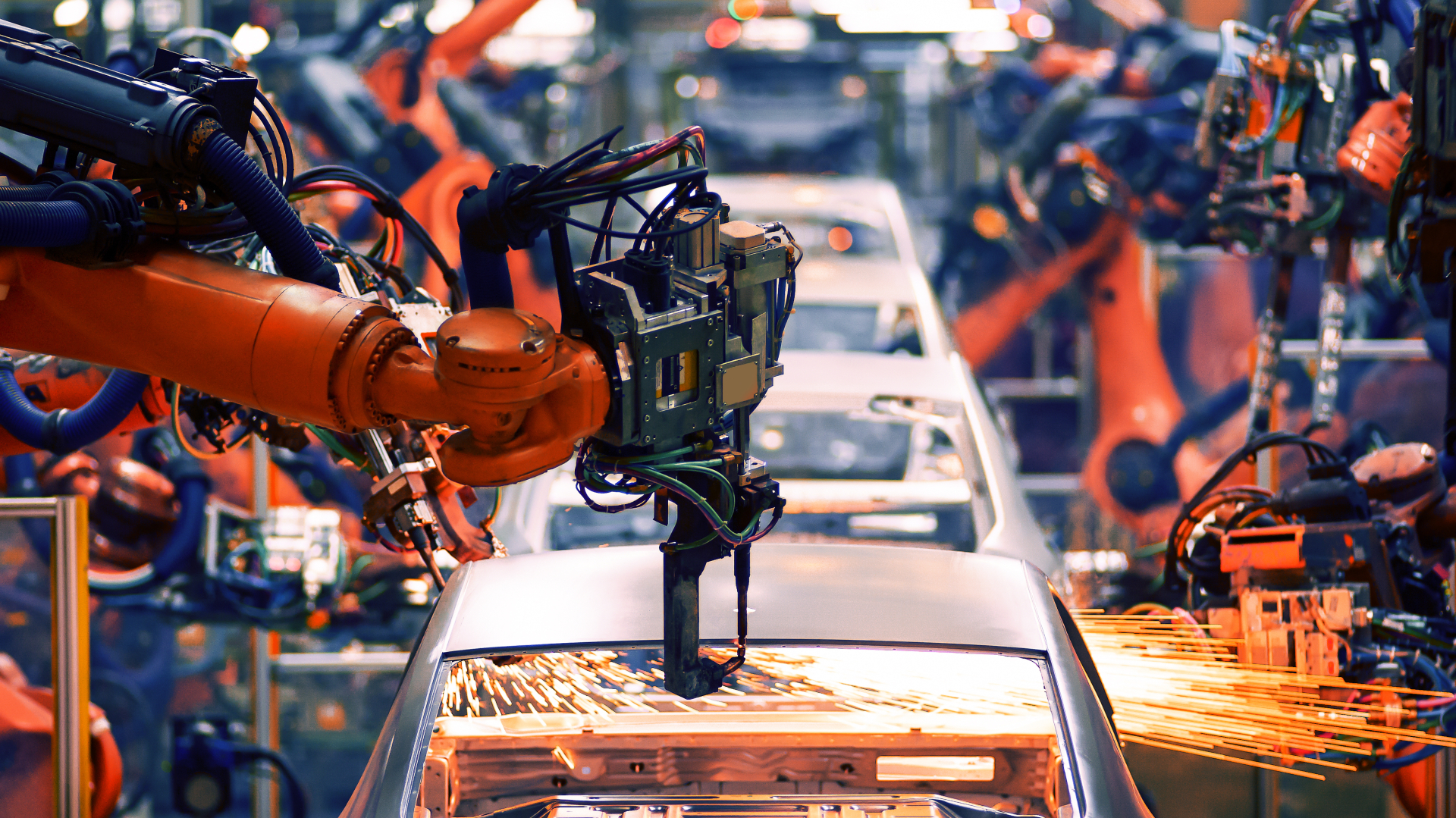
Automation Industry
Plasma cutting is essential for making parts for robotics and automation systems, enabling fast, precise cutting of metal components for robotic arms and industrial machinery.
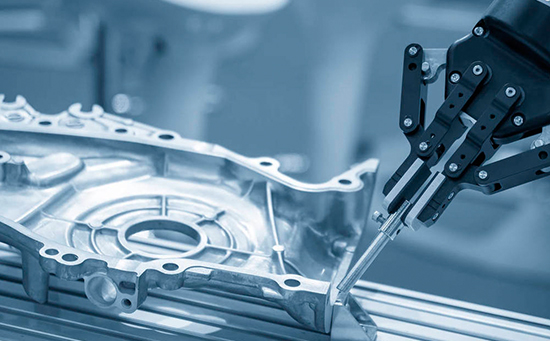
Robotic Parts
Plasma cutting is used to manufacture key robotic parts like arms, joints, brackets, and end effectors. Its precision, speed, and ability to handle various materials make it ideal for efficient, cost-effective production.
If you are looking for a rapid prototyping manufacturer or CNC machine shop to manufacture low-volume, medium-volume, or mass-production products, NOBLE is the ideal choice. Our well-trained and experienced staff manufactures all sizes of parts according to drawings on modern sheet metal processing equipment with the highest precision and processing quality. In addition, we provide professional design considerations for your sheet metal machining projects.
Want to get the most professional and fast service for your sheet metal processing project? Upload your CAD file and get a quote now!
Sheet Metal Plasma Cutting of FAQs
Sheet metal Plasma cutting is one of the processes NOBLE are proud of. that uses a high-velocity jet of ionized gas (plasma) to melt and blow away material, usually metal. An electric arc passes through compressed air or gas, turning it into plasma and creating a focused, high-temperature cutting stream. This method is commonly used for cutting electrically conductive materials like steel, aluminum, brass, and copper.
Sheet metal plasma cutting ionizes gas (air, nitrogen, or oxygen) to create high-energy plasma, which melts and blows away material. The process uses intense heat for precise, clean cuts with minimal distortion.
Metals like tungsten, titanium, hardened steel, and Inconel are challenging to cut due to their hardness, high melting points, and toughness. Specialized methods like water jet, EDM, and abrasive cutting are often required.
Plasma cutting offers clean cuts but may require additional finishing for smoother edges. It only works on conductive metals, has limitations with thick materials, and poses safety risks, requiring protective measures.
Choosing a cutting process depends on material type, thickness, precision needs, speed, and cost. Plasma suits medium metals, laser excels in precision for thin materials, while water jet is versatile and heat-free.
The choice of plasma cutting gas significantly influences cutting speed, edge quality, and material compatibility.
- Airis cost-effective for general cutting, especially on carbon steels, but may result in rough edges.
- Nitrogenoffers cleaner cuts, reducing oxidation, and is ideal for stainless steel and non-ferrous metals.
- Oxygenenhances cutting speed on carbon steel but may cause more oxidation and rougher edges.
- Argonand its mixtures provide high-quality cuts for aluminum and other non-ferrous metals with minimal oxidation
- Hydrogen(often mixed with argon) allows for faster, high-quality cuts on stainless steel, though it’s more expensive. The choice depends on material type, thickness, required quality, and cost considerations.
Optimizing plasma cutting involves adjusting parameters (amperage, speed), selecting the right gas (e.g., nitrogen for stainless steel), maintaining consumables, ensuring arc stability, and using CNC systems for precision. Balancing speed and quality requires ongoing calibration and optimization.
For high-precision cutting, use fine plasma systems, integrate CNC for precise control, select specialized gases like nitrogen for clean edges, and minimize post-processing. These steps help achieve smoother cuts, reduce material distortion, and maintain tight tolerances.