Wire EDM Services
Our Custom Wire EDM Services
Providing flawless wire EDM parts solutions for complex geometries at competitive prices, with extensive wire-cutting experience, get a quote in minutes and unmatched high-precision wire EDM parts in days!
- Advanced Equipment & Competitive Price
- ISO 9001 & ISO13485 Certified Factory
- 10+ Years of Wire EDM
- Instant Auto Threading With Enhanced Thermal Stability
- Lead Time As Fast As 3 Days
- 24/7 Engineering Support
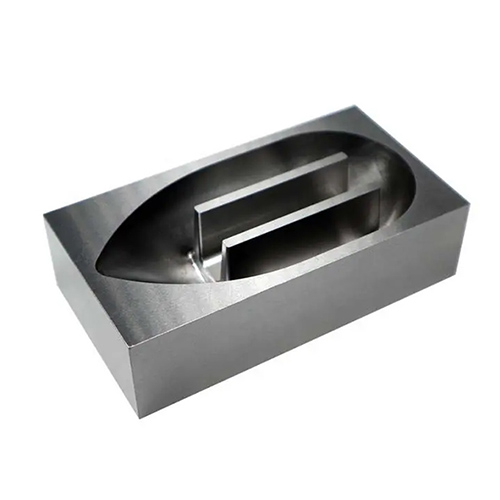
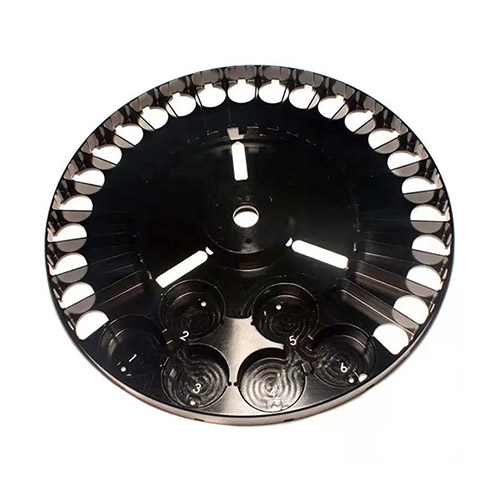
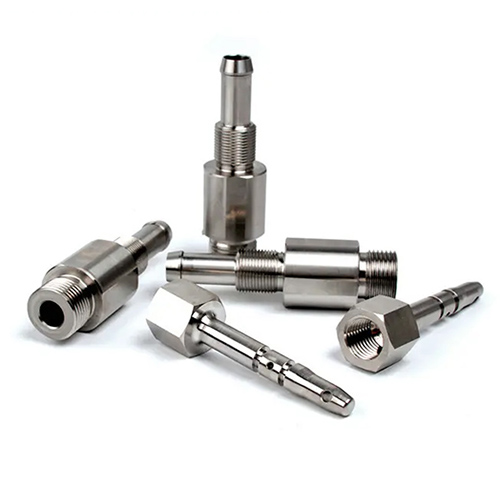
STEP | STP | STL | IGS | IGES | PRT | SLDPRT | SAT | X_T | IPT | CATPART | PDF
Max. file size: ≤20MB
- All uploads are secure and confidential.
Our Powerful Wire EDM Processes
NOBLE is a Wire EDM manufacturer with more than ten years of experience. Wire EDM is an erosion process rather than other subtractive processes that rely on cutting. Therefore, it has different surface properties that often depend on the number of passes (iterative cuts) to achieve the best finish. Our wire EDM process is as follows:
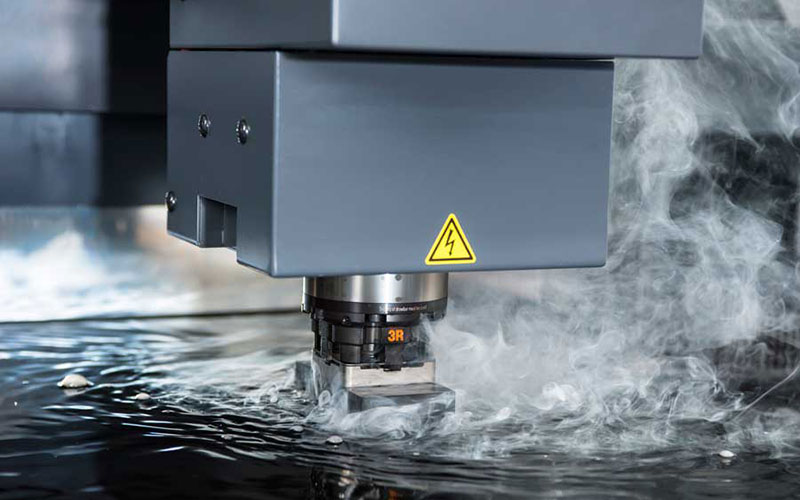
NOBLE Wire EDM suppliers can handle rougher surface preparations and quickly achieve designs with tolerances of +/- .002’. Meeting approximately 90% of Wire EDM parts requires only the first pass, but the tolerances are acceptable for many applications and surface finishing requirements.
- 100% Part Inspection
- Precision Wire EDM Machines
- Hard & Conductive Materials
- Competitive & Affordable Price
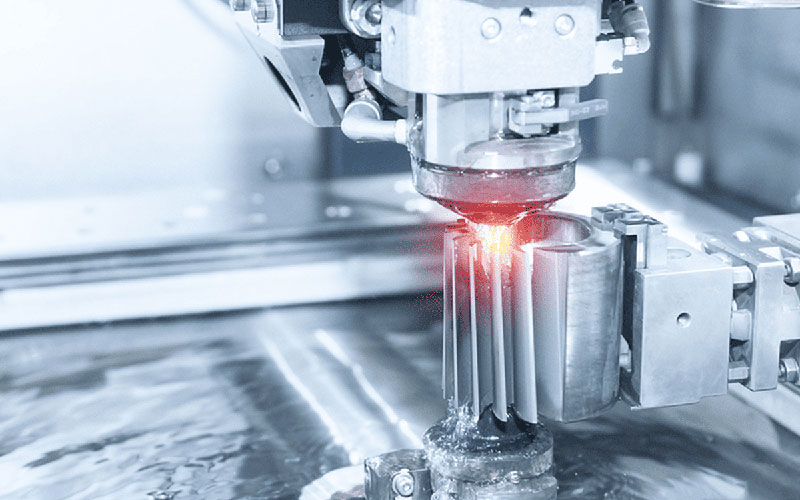
For more advanced customer requirements, NOBLE Wire EDM manufacturers perform a more refined second-step process that can achieve tolerances up to +/- 0.0005″ and a surface finish of 72 µin that is virtually indistinguishable to the naked eye.
- No Tooling Wear
- Direct Delivery to You
- Cut the Hardest Materials
- Unmatched Precision & Intricacy
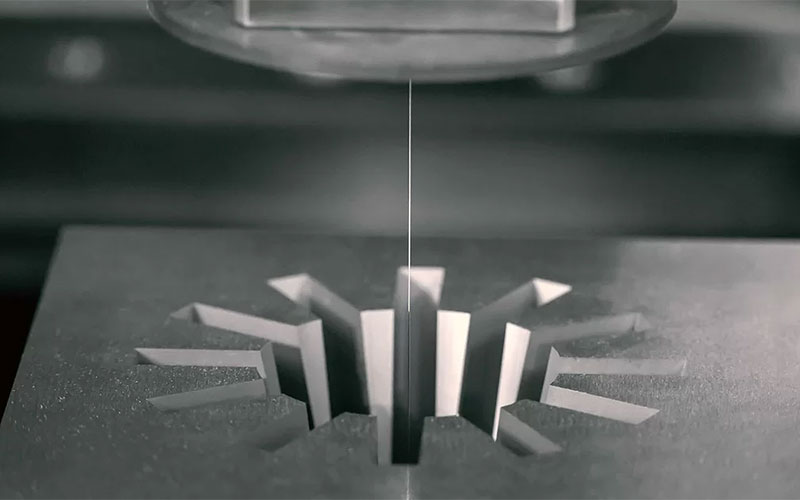
For the most delicate wire cuts and finest finishes required for highly sensitive applications such as medical device parts and aerospace parts. In the third step, NOBLE Wire EDM manufacturers will reduce the surface finish to 35 µin, which can basically exceed many customer expectations and requirements.
- High-volume Production
- Tolerances to +/-.0001”
- Efficient Production
- Versatility and Cost-effective
Our Robust Wire EDM Capabilities
From Prototyping to Manufacturing
NOBLE is an all-encompassing production platform created to meet all of your Wire EDM project demands.
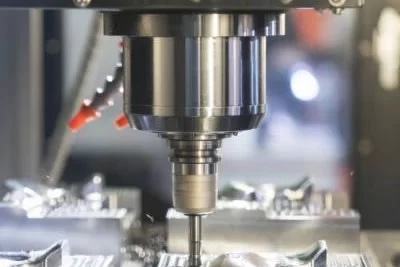
Rapid Prototyping
We recognise the value of precision and speed throughout the prototyping stage. You can quickly bring your ideas to life with the help of our Wire EDM services.
- Capability: 20-500
- Lead Time: 10 business days
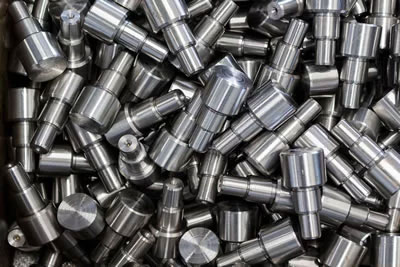
Low Volume Production
Low Volume Production enables them to test how their products will perform in the market before committing to larger orders. Additionally, small batch production can be beneficial for buyers looking for customized products. Even in small batch production, NOBLE not only has excellent quality, but also has favorable prices.
- Capability: 500-1000
- Lead Time: 15 business days
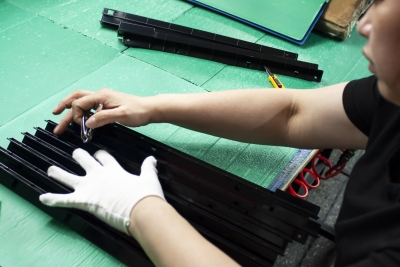
High Volume Manufacturing
To remain competitive in today’s fast-paced industrial environment, meeting high-volume production demands while maintaining quality and efficiency is critical. Our wire EDM services guarantee high volumeproduction as in low volume production.
- Capability: 1000+
- Lead Time: 20 business days

On-Demand Production
You will receive high precision and a high degree of quality products thanks to our comprehensive service for on-demand production orders. A higher manufacturing rate also enables the delivery of production parts precisely when they are needed.
- Capability: opitional
- Lead Time: depand your requirements
Why Choose Us for Custom Wire EDM Services
NOBLE combines the most advanced wire EDM technology with a team of experienced engineers, from prototype design to cutting and molding, and always provides customers with unparalleled high-precision wire EDM parts with stable performance at competitive prices. Quotation within minutes, fast delivery within days.
Strong Manufacturing Capabilities
As an ISO 9001 & ISO13485 certified factory, NOBLE has thousands of square meters of production workshops, more than 80 Wire EDM machines, a complete supply chain, and strict quality inspection processes, allowing you to get impeccable products at competitive prices. High-precision Wire EDM parts.
No MOQ
There is no minimum order requirement, which helps to quickly transfer Wire EDM parts from design to production, and reduces cutting costs through advanced Wire EDM technology and experienced engineers to meet your high-precision complex shape parts cutting needs.
High Precision Wire EDM Parts
State-of-the-art technology, strict and efficient quality management systemand dedicated team enable to offer ultimate precise parts based on your predefined project criteria.
Featured Customized Services
NOBLE uses advanced wire EDM equipment to ensure high-precision wire-cut parts. In addition, to meet your needs for high-precision wire EDM parts with complex shapes, our knowledgeable engineers and technicians can resolve your concerns and provide personalized customized wire EDM services for large and small businesses.
Work with Us in 4 Simple Steps Only
With many years of manufacturing experience, NOBLE offers the best solutions for all rapid prototyping and low-volume manufacturing needs. We streamline the innovation cycle into four simple but effective steps.



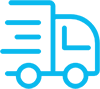
Wire EDM Part Size Standards
Parameter | Small Parts (mm) | Medium Parts (mm) | Large Parts (mm) |
Maximum Length | 50 | 100 | 500 |
Maximum Width | 30 | 70 | 300 |
Maximum Height | 10 | 40 | 150 |
Minimum Thickness | 0.5 | 1.0 | 5.0 |
Tolerance | ±0.005 | ±0.01 | ±0.03 |
Materials for Custom Wire EDM Machining Parts
Provide customers with customized Wire EDM parts solutions at competitive prices, and get the Wire EDM parts you expect in a short time. NOBLE Wire EDM manufacturers can cut the following materials:
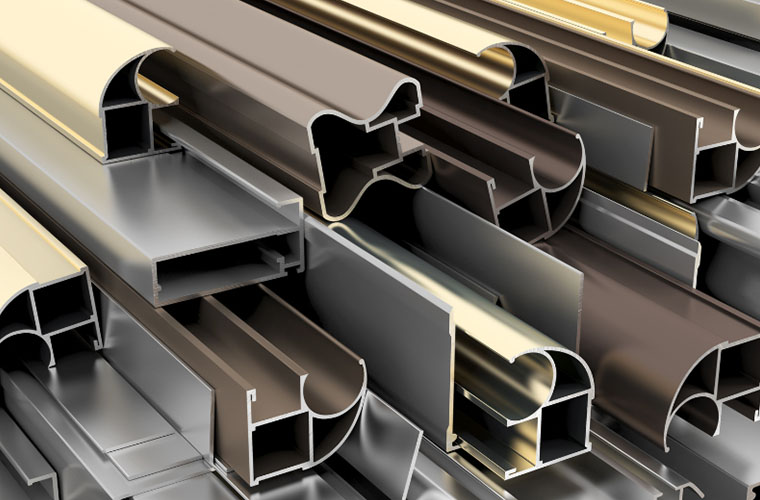
Aluminum
Aluminum, being an electrically conductive material, can be effectively cut using wire Electrical Discharge Machining (EDM). Wire EDM allows for the precise shaping and cutting of aluminum, making it suitable for various industries that require accurate and intricate parts made from this lightweight metal.
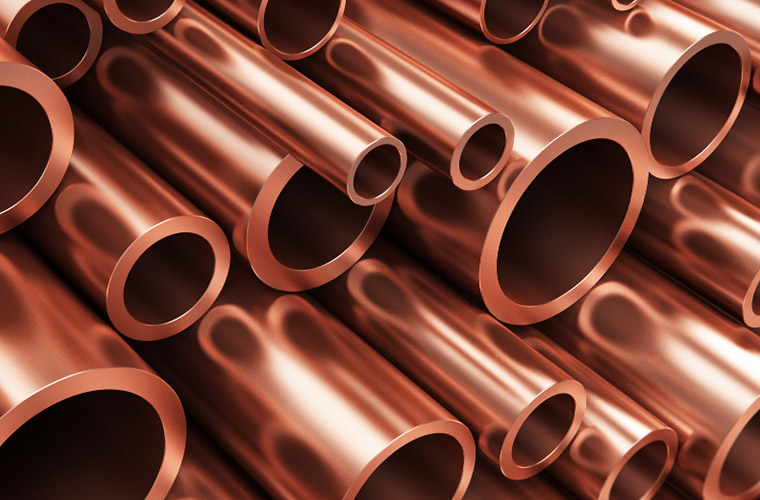
Copper
Wire EDM efficiently cuts copper, allowing for precise and intricate shapes to be formed. Wire EDM ensures accurate and repeatable cuts in copper, maintaining tight tolerances and excellent surface finishes. The process minimizes heat-affected zones and material distortion, preserving the inherent properties of copper.
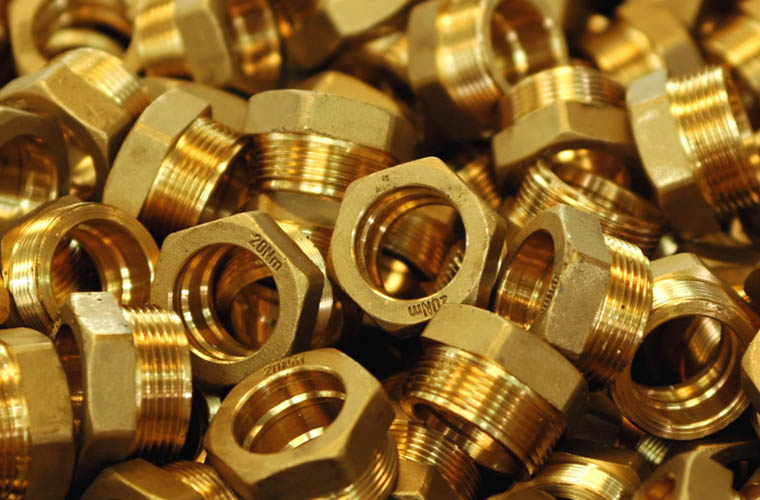
Brass
The high conductivity of brass allows for efficient and controlled electrical discharges during the EDM process. Its favorable machinability characteristics, including good cutting performance and chip formation, make it suitable for wire EDM operations. Brass also offers good thermal conductivity, aiding in the dissipation of heat during the machining process. These properties, combined with the ability to achieve precise cuts and intricate shapes, make brass a versatile and effective material for wire EDM applications.
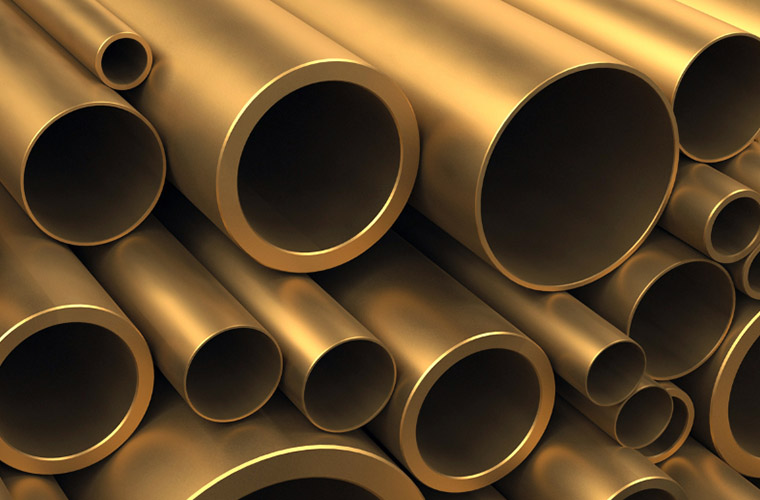
Bronze
The conductivity of bronze is suitable for wire EDM. Its machinability characteristics, such as good chip formation and cutting performance, make it suitable for wire EDM operations. Bronze also offers excellent heat dissipation properties, helping to manage the heat generated during machining. With its combination of conductivity, machinability, and heat dissipation, bronze is a viable material choice for wire EDM, allowing for precise cutting and shaping of components.
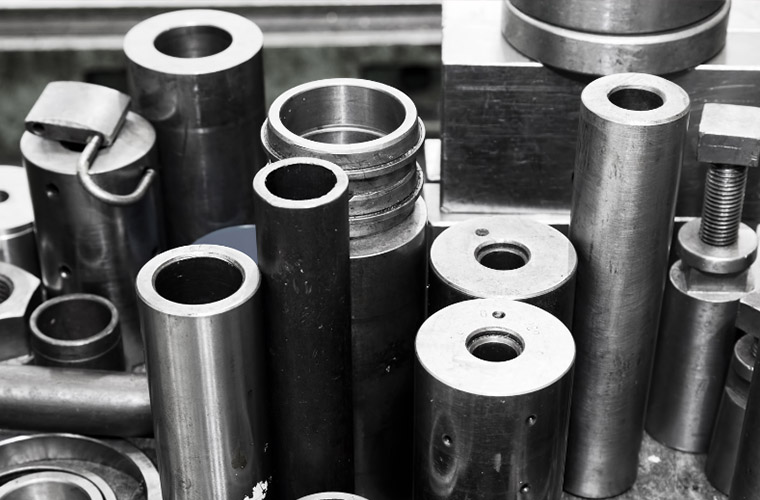
Steel
Steel is a widely used material in wire Electrical Discharge Machining (EDM) due to its electrical conductivity and versatility. Steel offers excellent strength and durability, making it suitable for a wide range of applications. Steel’s machinability allows for efficient material removal, while its ability to withstand high temperatures makes it compatible with the heat generated during EDM. With these properties, steel is a reliable choice for wire EDM, offering the ability to produce intricate parts with tight tolerances in various industries.
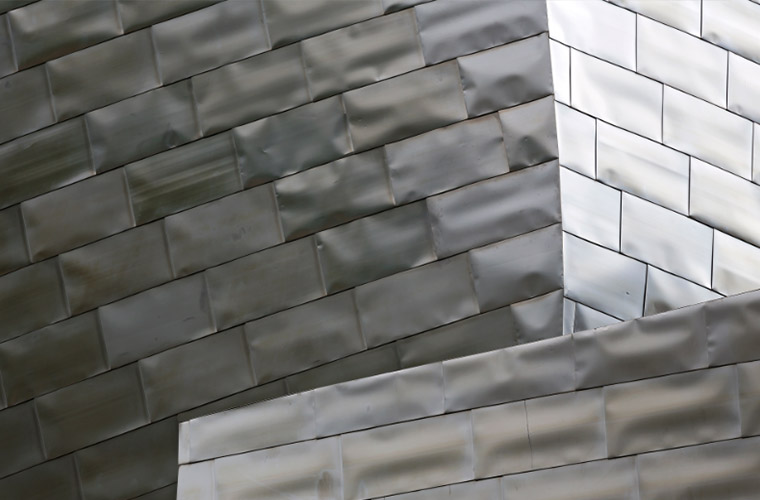
Titanium
Titanium has a number of material properties that make it the ideal metal for demanding applications. These properties include excellent resistance to corrosion, chemicals and extreme temperatures. The metal also has an excellent strength-to-weight ratio.
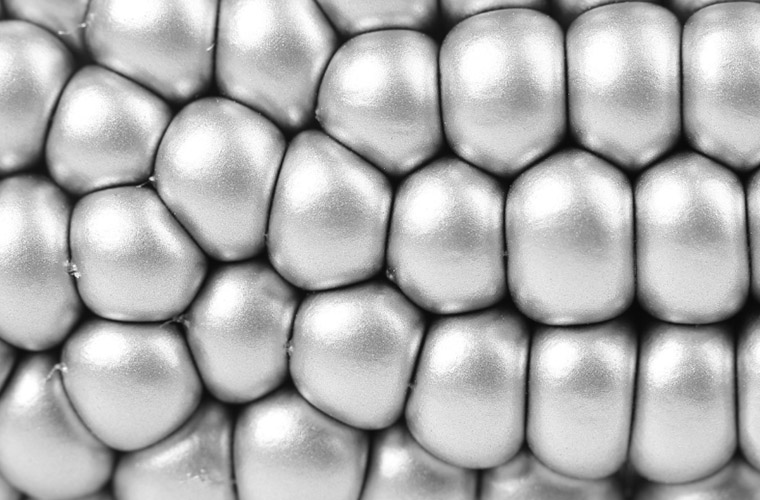
Other Conductive Materials
Our Wire EDM capabilities go beyond the typical materials, aside from the common materials. We are skilled in working with a variety of nickel alloys as well as precious metals like gold and silver. Whatever your unique material needs are, we have the know-how to produce excellent outcomes.
Surface Finishes for Wire EDM
NOBLE Wire EDM manufacturer offers a wide range of surface finishing options to help your Wire EDM parts look better. The surface finish of your custom Wire EDM part is designed to enhance properties such as appearance, surface hardness, surface roughness, chemical resistance, and corrosion resistance. They also help mask any obvious knife marks in areas cut with power knives. Listed below are some of your best Wire EDM part surface finishing.
Anodizing
Anodizing improves corrosion resistance, enhancing wear resistance and hardness, and protecting the metal surface. Widely used in mechanical parts, aircraft, and automobile parts, precision instruments, etc.
Materials: Aluminum
Color: Clear, black, grey, red, blue, gold.
Texture: Smooth, matte finish
Powder Coating
Powder coating is a type of coating that is applied as a free-flowing, dry powder. Unlike conventional liquid paint which is delivered via an evaporating solvent, powder coating is typically applied electrostatically and then cured under heat or with ultraviolet light.
Materials: Aluminum, Stainless Steel, Steel
Color: Black, any RAL code or Pantone number
Texture: Gloss or semi-gloss
Electroplating
Electroplating can be functional, decorative or corrosion-related. Many industries use the process, including the automotive sector, in which chrome-plating of steel automobile parts is common.
Materials: Aluminum, steel, Stainless Steel
Color: N/A
Texture: Smooth, Glossy finish
Polishing
Polishing is the process of creating a smooth and shiny surface, either through physical rubbing of the part or by chemical interference. The process produces a surface with significant specular reflection, but in some materials is able to reduce diffuse reflection.
Materials: Aluminum, Brass, Stainless Steel, Steel
Color: N/A
Texture: Glossy
Brushing
Brushing is a surface treatment process in which abrasive belts are used to draw traces on the surface of a material, usually for aesthetic purposes.
Materials: ABS, Aluminum, Brass, Stainless Steel, Steel
Color: N/A
Texture: Satin
Custom Wire EDM Parts Display
Please browse through our extensive gallery showcasing precision Wire EDM created by our esteemed customers.
See What Our Customers Say About Us
The feedback of customers has a greater impact than a company’s advertising. Take a look at what our satisfied customers have to say about how we met their needs.
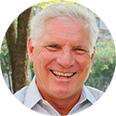
António
Automotivre engineer
The wire EDM service provided by NOBLE has been a aame-changer for our automotive manufacturina businessTheir expertise in cuttina a varietv of materials, including exotic allovs, has allowed us to push the boundaries ofdesian, The accuracy and attention to detailin their work have sianifcantly improved the cuality of our componentsTheir eficient turnaround time and competitive pricing make them our go-to choice for wire EDM services.
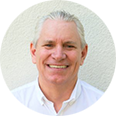
John
aerospace engineer
I needed precise and intricate parts for my aerospace project and inguired NOBLE , they advised the wire EDMservice for me. lt exceeded my expectations. They delivered exceptional accuracy and tioht tolerances, ensuring aperfect fit for my components. The surface finishes were fiawless, and the team demonstrated excellent attentionto detail. l highly recommend their wire EDM services for any complex machining need.
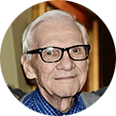
Jonathan
Mechanical Engineer
The wire EDM service provided outstanding results for our tool and die manufacturing company. NOBLE’s expertisein cuting hardened steel allowed us to achieve complex shapes with ease. The accuracy and repeatability of theilcuts were remarkable, saving us time and effort during the production process. Their commitment to quality andcustomersatisfactionis trulycommendable.
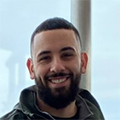
Simon
CEO
As a medical device manufacturer, precision is crucial for us. We turned to the wire EDl service, and they deliveredbeyond our expectations. Their ability to cut intricate features and maintain tight tolerances was remarkable. Thefinished parts had excellent surface finishes, eliminating the need for additional post-processing. Their wire EDM service has become an integral part of our production process, and we highly recommend NOBLE to others in the
industry.
What is Wire EDM?
Wire electrical discharge machining cuts or shapes metal workpieces using a thin electrode wire controlled by a CNC. Sparks develop between the wire and the workpiece as a result of the electric current charging the wire, melting the workpiece’s surface. Since the cutting wire never makes direct touch with the workpiece, neither the cutting path nor the shape of the material is altered. With its ability to produce intricate shapes, close tolerances, and superior surface finishes, wire EDM is perfect for hard and complex materials. However, mastering wire EDM is not simple. It requires expertise to ensure consistent, high-quality results. NOBLE leverages years of experience and innovation to unleash the potential of wire EDM, ensuring our customers receive the unparalleled solutions they deserve.
Wire EDM Applications
Because CNC machining can achieve high precision without changing the material structure with good manufacturing speed, it is becoming growing common as the range of machines, control systems, and tools for CNC machining continues to expand.NOBLE is dedicated to providing precision machining services for various industries and our precision CNC-crafted parts can be found in all areas of the industry, including.

Oil & Gas
Utilize top-of-the-line Wire EDM machines to optimise your energy components for dependability and efficiency.
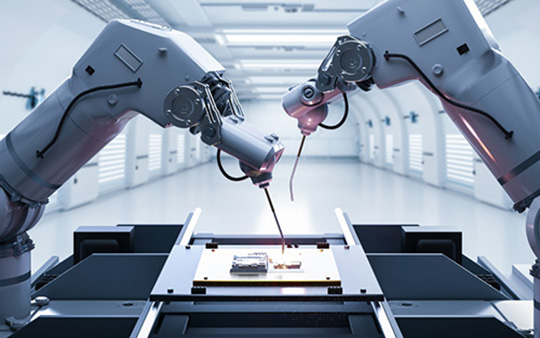
Automation Equipment
NOBLE Rapid Prototyping service allows you to quickly and easily create automated functional prototypes to test and optimize your design, select the right process, reduce costs, and shorten project cycles. On-demand services can produce automated parts with a high level of accuracy.
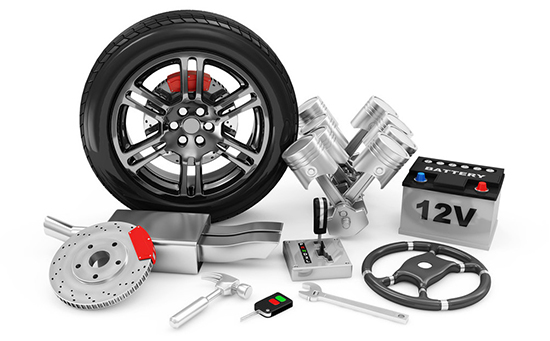
Automotive
Our Wire EDM services enables the production of a wide range of components that contribute to the performance, safety, and aesthetics of vehicles in the automotive industry.
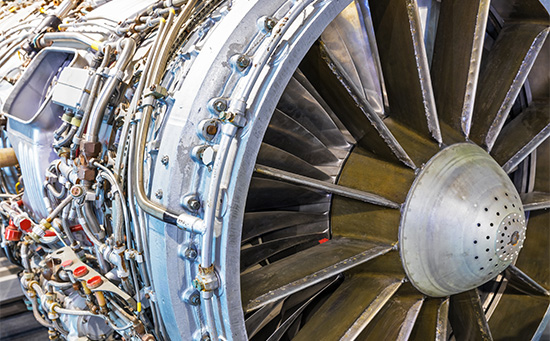
Aerospace
The experts at NOBLE have in-depth knowledge of Wire EDM methods for the aerospace sector. Utilize our Wire EDM capabilities to create lightweight, highly durable components without sacrificing strict aviation standards.
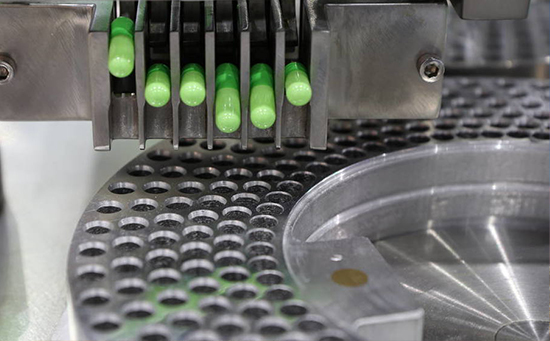
Medical Devices
Our Wire EDM services have been meticulously designed to meet the precision and cleanness of the medical industry, ensuring that every component we produce meets or exceeds the highest standad.
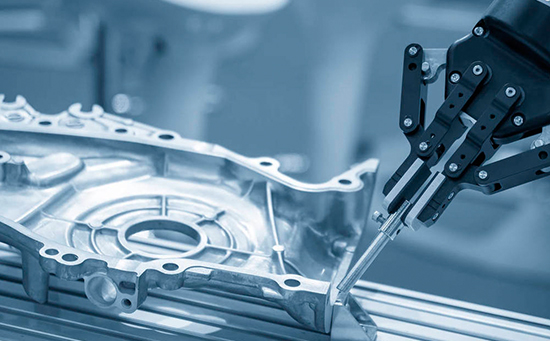
Robotics
Our cutting-edge capabilities, innovative craftsmanship, and skilled engineering team could better serve the robotics field with advanced metal Wire EDM solutions.
If you are looking for a rapid prototyping manufacturer or a CNC machine shop to fabricate small, medium-volume, or mass-production products, NOBLE is an ideal choice.Our well-trained and experienced staff manufactures parts in line with drawings on modern CNC machines, with the highest accuracy and processing quality in all sizes.In addition, we provide professional design considerations for your CNC machining projects.
Want to get the most professional and fastest service for your CNC machining project? Upload your CAD files now and obtain a quote!
Wire EDM FAQs
Wire Electrical Discharge Machining (EDM) is a precision machining process that uses a thin, electrically conductive wire to cut or shape materials. The wire is guided through the workpiece with computer-controlled movements, while an electrical discharge creates intense heat, melting and vaporizing the material. A dielectric fluid cools and flushes away debris. Wire EDM is ideal for hard and complex materials, allowing for intricate shapes, tight tolerances, and excellent surface finishes. However, it can be slower than other methods and requires skilled operators. It is commonly used in industries like aerospace, automotive, and medical device manufacturing.
A CNC control device that can move the wire on a three-dimensional axis for greater flexibility controls the wire-cut EDM machine. Wire-cut EDM can be used to create more intricate patterns and smaller angles than conventional EDM. Complex cuts are possible with a more precise cutting technique.
Wire Electrical Discharge Machining (EDM) achieves high accuracy due to several factors. Firstly, the wire used in EDM is extremely thin, typically ranging from 0.1 to 0.3 mm in diameter. This thinness allows for precise cutting and intricate shapes. Secondly, the wire EDM process is controlled by computer numerical control (CNC) systems, which provide precise and accurate movement of the wire along programmed paths. Additionally, the dielectric fluid used in wire EDM serves to cool the workpiece and flush away debris, ensuring a consistent and controlled machining environment. These factors, combined with the ability to program complex shapes, contribute to the exceptional accuracy achievable with wire EDM.
The difference is speed. Up to 0.25′′ in thickness, laser cutting delivers quick cutting speeds. Even though wire EDM gives greater precision than laser cutting, it is frequently slower.
Wire Electrical Discharge Machining (EDM) is capable of cutting a wide range of electrically conductive materials. These include but are not limited to metals such as hardened steel, stainless steel, aluminum, titanium, copper, brass, and exotic alloys. Wire EDM is also effective in cutting conductive ceramics and some non-conductive materials with the aid of special techniques. This machining process is particularly advantageous for materials that are difficult to machine with conventional methods due to their hardness, toughness, or heat resistance. It finds applications in industries such as aerospace, automotive, electronics, tool and die manufacturing, and medical device manufacturing, where precision, intricate shapes, and tight tolerances are required.
Wire EDM machines can also cut through a variety of metal types with little effort because they can handle both ferrous and non-ferrous metals, as well as polymers and rubber that aren’t suited for conventional EDM machines.
Yes, wire Electrical Discharge Machining (EDM) is capable of making holes. This process is often referred to as wire EDM drilling or EDM hole drilling. In EDM hole drilling, a small-diameter wire electrode is used to create precise, round holes in electrically conductive materials. EDM hole drilling is commonly used in various industries, including aerospace, automotive, and medical, where high precision and accuracy are required for applications such as cooling holes, ejector holes, and small-diameter holes in intricate components.