Vacuum Casting Services
Our Custom Vacuum Casting Services
Provide reliable custom vacuum casting services from prototyping to low-volume part manufacturing at competitive prices. High precision and stable performance vacuum forged parts have excellent quality and faster turnaround time.
- Advanced Equipment & Cost-Effective Price
- ISO 9001 & ISO13485 Certified Factory
- 10+ Years of Vacuum Casting Service
- Lead Time As Fast As 3 Days
- 24/7 Engineering Support
- Instant Vacuum Casting Services Quotes
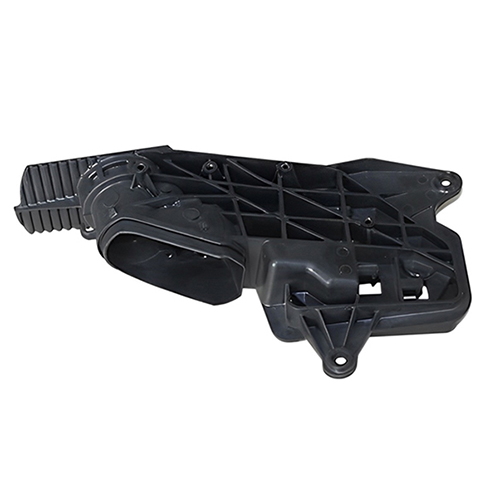
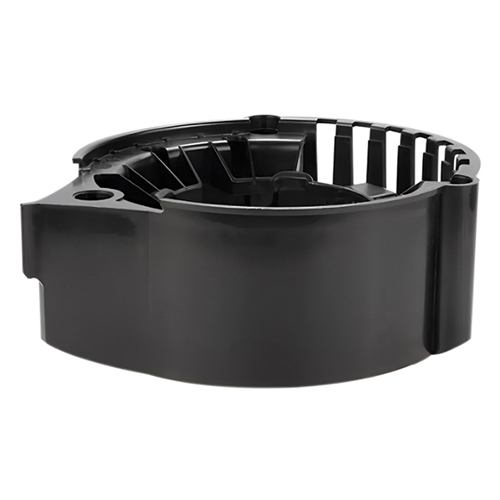
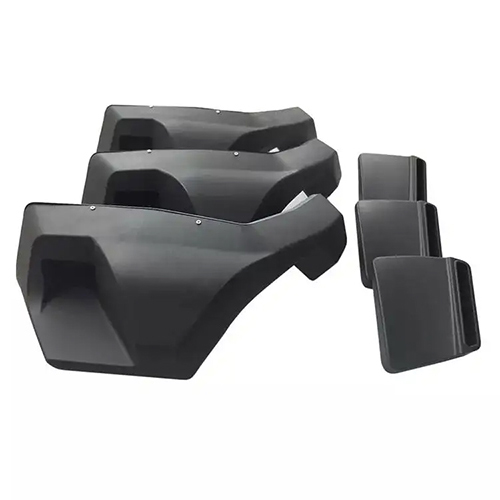
STEP | STP | STL | IGS | IGES | PRT | SLDPRT | SAT | X_T | IPT | CATPART | PDF
Max. file size: ≤20MB
- All uploads are secure and confidential.
Our Powerful CNC Machining Processes
Providing custom CNC machining solutions at competitive prices, we choose from over 100 materials and 60+ surface finishes to ensure you receive high-precision, structurally complex, and performance-stable parts. Try our precision CNC machining services and become our next satisfied customer.
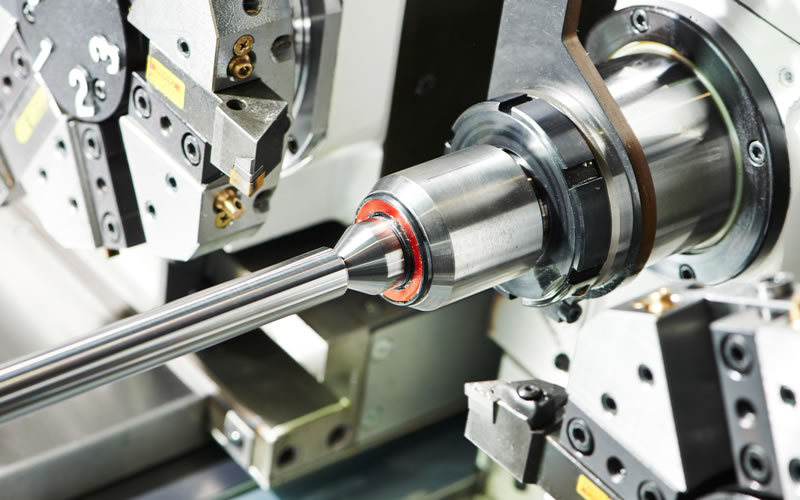
CNC turning is the process of cutting metal or plastic parts with cylindrical features from the outside of a bar with a rotating tool. The turning process can effectively manufacture circular parts and can be applied to create parts with complex internal and external geometries and various threads.
- Tolerances Down to ± 0.0003 In.
- Competitive Price 30% Cost Save
- Fast Turnaround in 7 days
- Quick Turn Milling Services
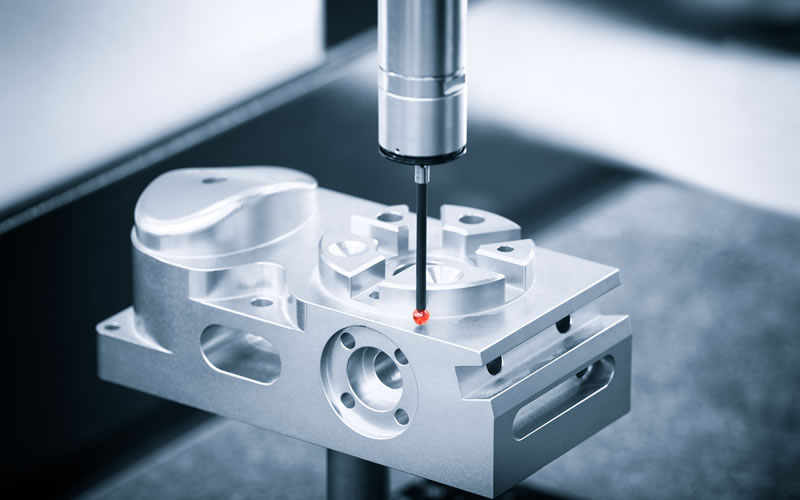
CNC milling is a subtractive process that uses 3-, 4-, and 5-axis milling machines and a variety of cutting tools to remove material from solid blocks of plastic and metal into final parts with varying geometries. With our 3-axis and 5-axis CNC milling services, you will be able to get milled parts with a tolerance of 0. 01mm.
- Tolerances Down to ± 0.0002 In.
- Quote Within 24 hours
- Fast Turnaround in 7 days
- Quick Turn Turning Services
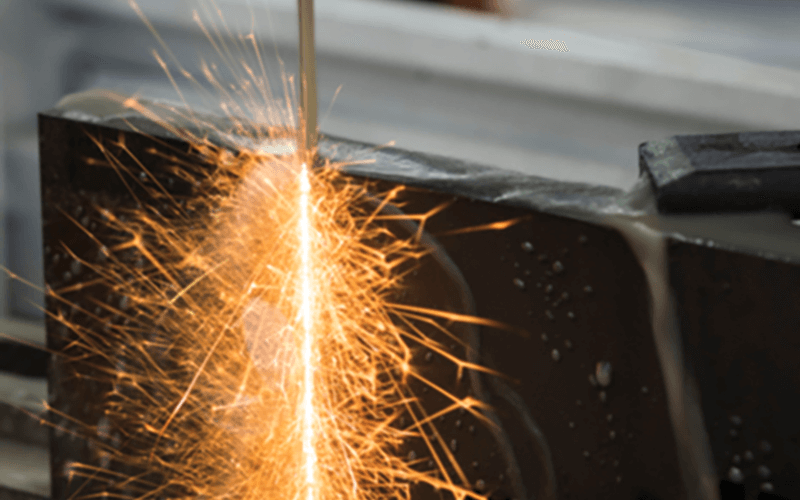
EDM and wire-cutting are CNC machining processes that use copper, graphite, or molybdenum wire to get the desired design for undercuts, sharp corners, and the removal of unnecessary material from workpieces. EDM is also frequently used to produce mold and rapid tooling.
- State-of-the-art Equipment
- 10+ Years of EDM & Wire-Cut
- Fast Turnaround in 7 days
- 1-to-1 Quote Analysis
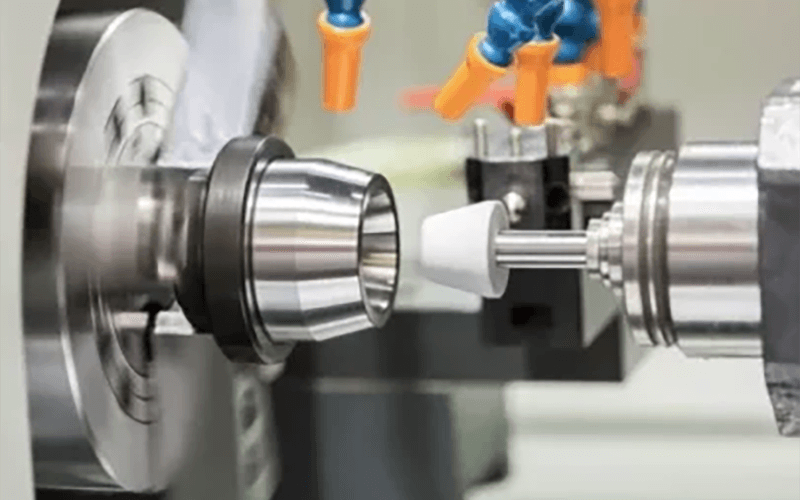
Our CNC grinding machining service will be your best option if you need a very flat surface item or a round part with tolerances of OD and ID ±0.005mm for your production demands.
- Tolerances Down to ± 0.0005 mm.
- Competitive Price 30% Cost Save
- Fast Turnaround in 7 days
- Quick Turn Grinding Services.
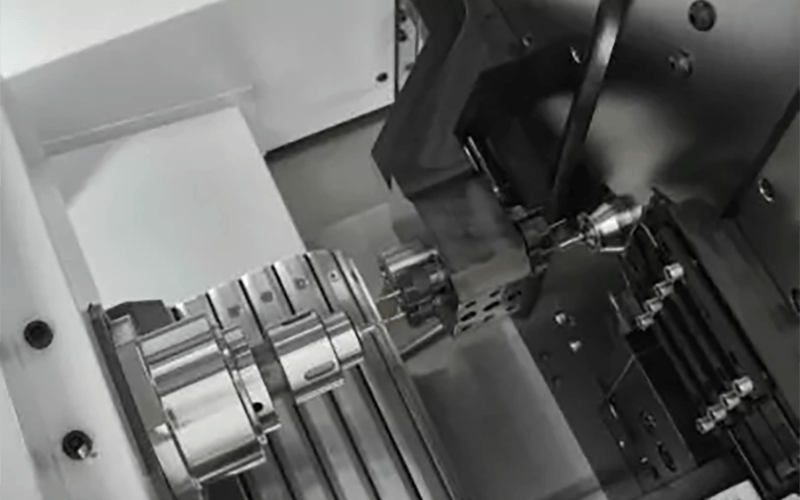
Swiss machining is a productive method for creating thin or complex parts. We can always cut the material that is near the workpiece holder by moving the workpiece as well as the active tooling. To prevent distortion in contrast to a conventional CNC lathe.
- Tolerances Down to ± 0.0005 mm.
- Competitive Price 30% Cost Save
- Fast Turnaround in 7 days
- Quick Turn Swiss Machining Services.
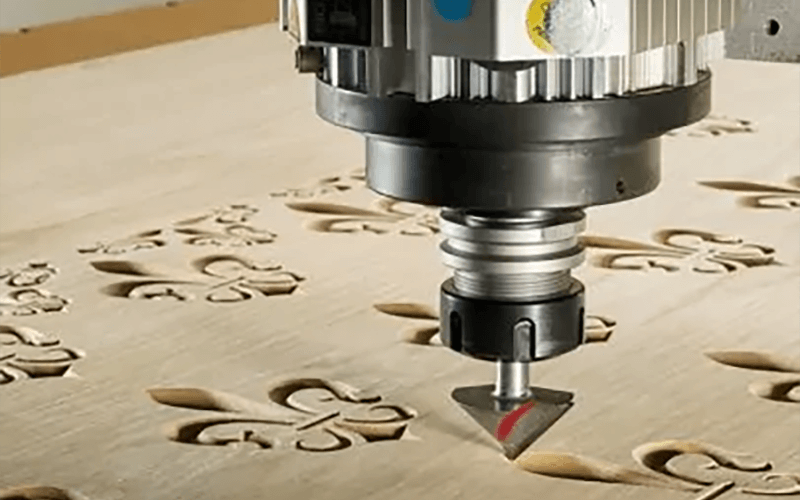
We provide CNC routing services for prototypes and parts machining of soft materials like EPS foam, EVA, and wood in addition to regular milling services for parts made of engineering plastics or metals.
- 10+ Years of CNC Routing
- Competitive & Affordable Price
- 100% Part Inspection
- Fast Turnaround in 7 days
Our Robust Vacuum Casting Capabilities
From Prototyping to Manufacturing
NOBLE is your trusted one-stop custom manufacturing solution, from prototype design to manufacturing, through huge manufacturing resources, suitable technology, streamlined process, expert guidance, and perfect quality inspection process to turn your ideas into reality.
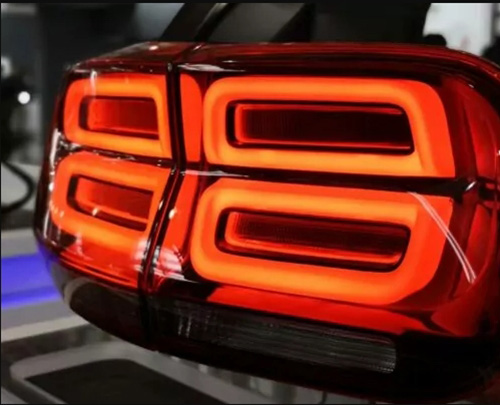
Prototype Machining
From NOBLE, get an online quote with free design analysis in hours to get your CNC machined prototypes done in days.
- State-of-the-art Equipment
- 10+ Years of CNC Machining
- Competitive & Affordable Price
- Quote Within 24 hours
- Free DFM Feedback
- Fast Turnaround in 7 days
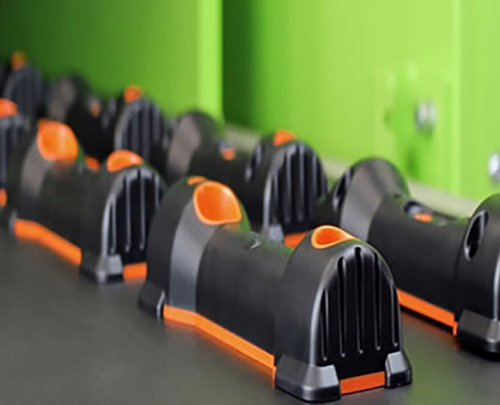
Low-Volume Manufacturing
With advanced production equipment and an experienced team of engineers, we can manufacture products with complex geometric shapes and high precision requirements with strict tolerance control and perfect quality inspection processes.
- Competitive & Affordable Price
- State-of-the-art Equipment
- 10+ Years of Low-Volume Manufacturing
- Fast Lead Time
- 30+ Countries shipped
- 100% Part Inspection
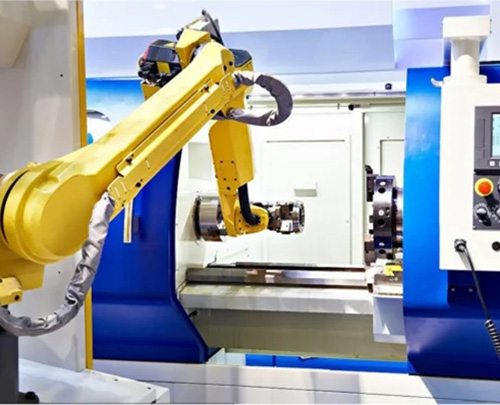
Medium & Mass Production
NOBLE meets mass production needs through strict tolerance control, quality inspection, and a complete supply chain, and quickly delivers cost-effective, high-precision parts.
- 10+ Years of Medium&Mass Production
- Competitive & Affordable Price
- Large Supplier Network
- 100,0000+ Unique parts produced
- Guaranteed Consistent Quality
- Fast Turn-Around Production
Why Choose Us for Custom Vacuum Casting Services
By integrating cutting-edge technology with the knowledge of our qualified personnel, NOBLE prioritizes client happiness. Our vacuum casting process is precise, efficient, and cost-effective, yielding exceptional results. Choosing our vacuum casting will help your business reach new heights of success.
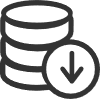
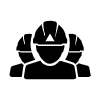
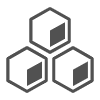
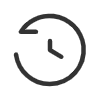
Work with Us in 4 Simple Steps Only
With many years of manufacturing experience, NOBLE offers the best solutions for all rapid prototyping and low-volume manufacturing needs. We streamline the innovation cycle into four simple but effective steps.



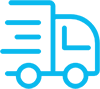
Vacuum Casting Tolerances and Standards
NOBLE offers a range of vacuum casting tolerances to meet your complex custom requirements. Depending on the master model and part geometry, we can achieve dimensional tolerances between 0.2 – 0.4 m. Below are the technical specifications for our custom vacuum casting services.
Type | Information |
Accuracy | Highest precision to reach ±0.05 mm |
Max Part Size | +/- 0.025 mm +/- 0.001 inch |
Minimum wall thickness | 1.5mm~2.5mm |
Quantities | 20-25 copies per mold |
Color & Finishing | Color and texture can be customized |
Typical Lead Time | Up to 20 parts in 15 days or less |
Materials for Vacuum Casting
You can choose a wide range of vacuum casting materials depending on the peculiarities of your project. Here are some choices for you:
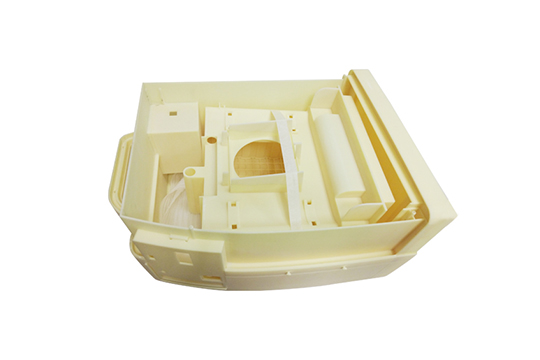
ABS
ABS is a thermoplastic polymer, is widely used due to its exceptional resistance to impact, temperature, and chemicals. It also offers a sleek surface finish and is easy to produce and handle.
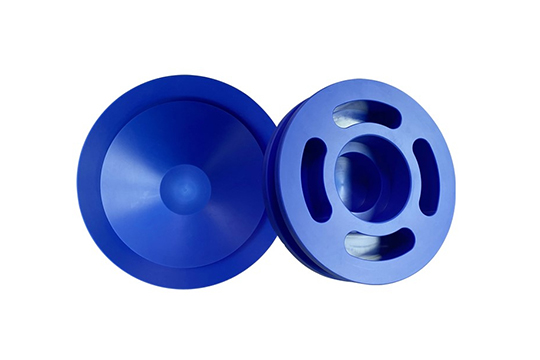
POM
POM, also known as acetal or Delrin, is a type of engineering thermoplastic that boasts exceptional dimensional stability, stiffness, temperature resistance, and impact resistance.
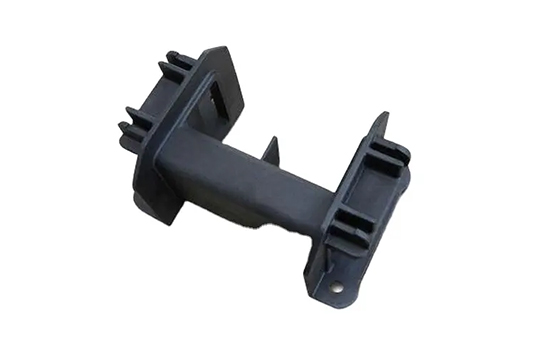
PP (Polypropylene)
Polypropylene (PP) is a material that is typically white and translucent and is resistant to corrosion while also possessing good toughness. Its most notable characteristic is its versatility, as it is suitable for use in a variety of processing methods and applications.
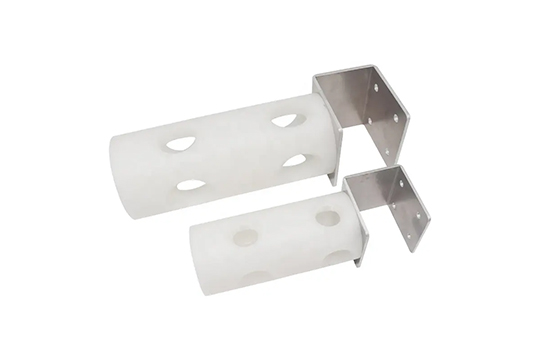
PE (Polyethylene)
Polyethylene is odorless, non-toxic, feels like wax, has excellent low-temperature resistance (minimum operating temperature can reach -100~-70°C), has good chemical stability, and can withstand most acid and alkali erosion (not resistant to oxidation) nature acid)
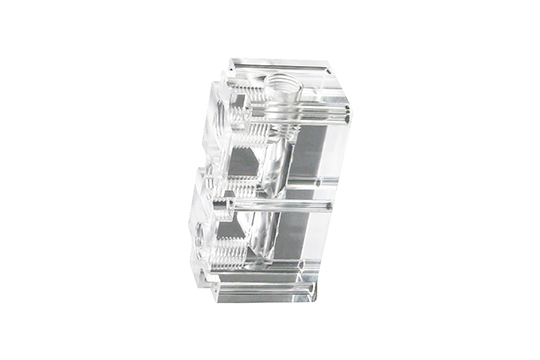
PC (Polycarbonate)
Polycarbonate (PC) is an amorphous thermoplastic known for its exceptional transparency and impact resistance. It also possesses strong electrical insulating properties and moderate chemical resistance.
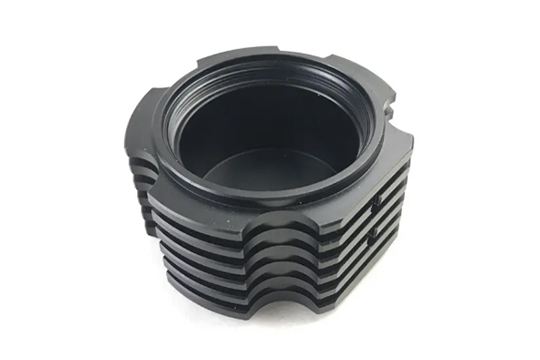
PMMA (Polymethylmethacrylate)
Polymethylmethacrylate, also named Acrylic. Acrylic is a highly versatile material known for its exceptional transparency, chemical stability, and resistance to heat, cold, and corrosion.
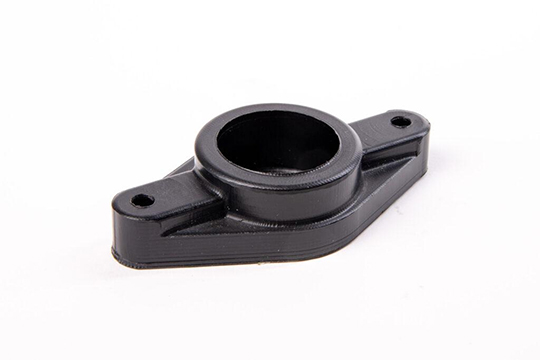
PEEK
PEEK boasts exceptional mechanical strength, self-lubrication, impact resistance, and flame retardancy. It is also highly resistant to acid, alkali, and other chemical corrosion, hydrolysis, wear, fatigue, stripping, and radiation.
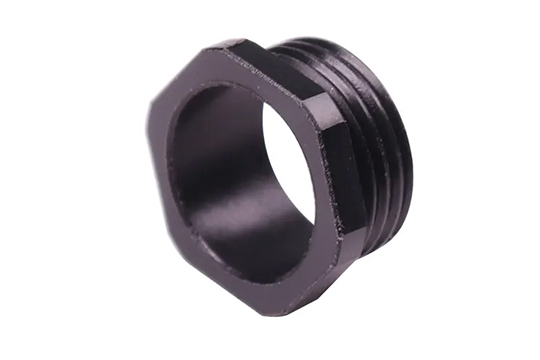
Nylon
Nylon is impressive mechanical properties such as heat and wear resistance, chemical resistance, and self-lubrication, polyamide fiber also possesses flame retardancy, a low coefficient of friction, and is easy to manufacture.
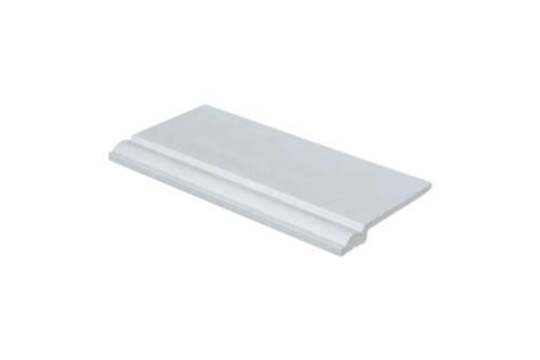
PS (Polystyrene)
Polystyrene (PS) is a polymer made from the monomer styrene, a liquid hydrocarbon that is commercially manufactured from petroleum. At room temperature, PS is normally a solid thermoplastic but can be melted at higher temperatures for molding or extrusion, and then resolidified.High-impact strength, low-cost resin with a wide range of options.
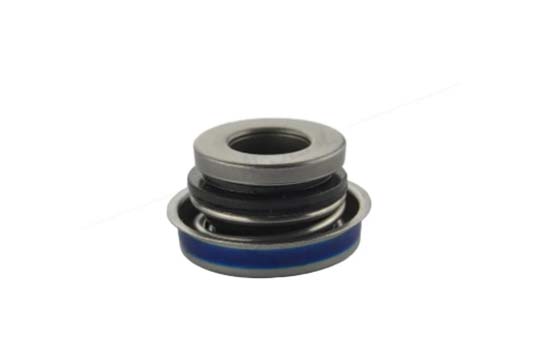
Elastomer
Elastomers are polymers with viscosity and elasticity and therefore are known as viscoelasticity. The molecules of elastomers held together by weak intermolecular forces generally exhibit low Young’s modulus and high yield strength or high failure strain. Examples are Natural rubber, Silicone Polyurethanes, and Polybutadiene, Polyurethane plastic resin.
Surface Finishes for Vacuum Casting
NOBLE can build unique surface layers for your vacuum casting parts using a wide range of surface finishes. These finishes assist you in meeting the aesthetic, toughness, and chemical resistance needs of your products. We can provide the following surface finishes based on your material selection and part application:
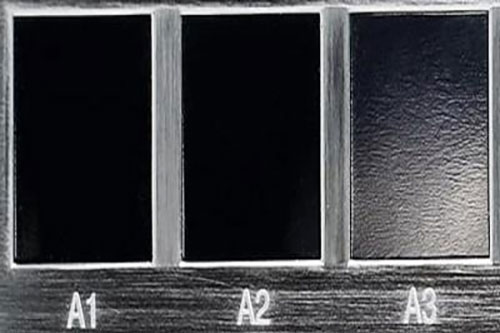
Glossy
A grade finishes are made using a diamond buffing process and yield shiny and glossy surfaces on injection molded parts.
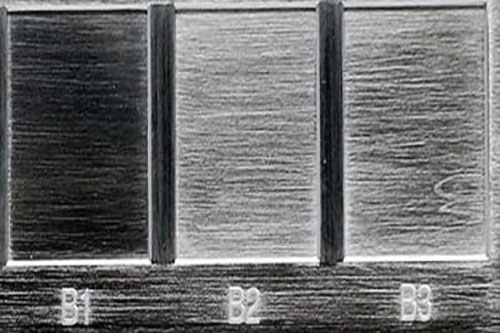
Semi-glossy
B grade finishes use grit sandpaper to produce parts with a slightly rougher finish than grade A parts. Custom molded plastic parts that undergo B grade finishing have a matte surface texture.
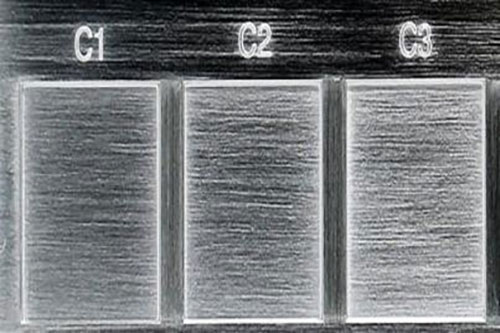
Matte
C grade finishes use grit sanding stones to produce a rough, uneven surface. Injection plastic parts that undergo C grade finishing have a matte surface texture.
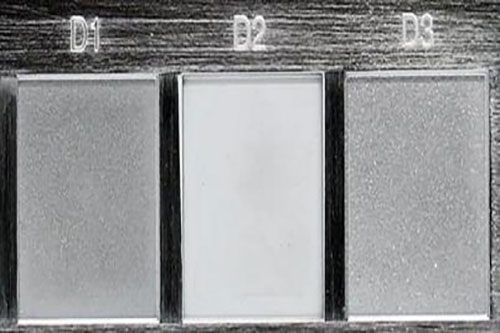
Textured
D grade finishes use grit and dry glass beads or oxide to produce a very rough textured finish. Depending on the type of material used, products can have a satin or dull finish.
Custom CNC Machining Parts Display
Check out our over a decade of precision custom CNC machined parts, including precision machined prototypes and parts from our valued customers.
Our Vacuum Casting Procedure
Vacuum casting is a cost-effective way to create high-quality prototypes and low-volume production parts with great detail and material options. Here are the steps involved:
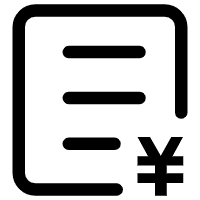
Step 1. Master Pattern Creation
The process begins with the creation of a master pattern, which serves as the original model for replication. The master pattern can be produced using various methods, such as 3D printing, CNC machining, or traditional fabrication techniques.

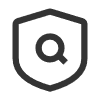
Step 2. Mold Preparation
A silicone mold is created around the master pattern. The mold is typically made in two halves, allowing for easy removal of the pattern and subsequent casting. The mold is then secured within a casting frame.

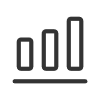
Step 3. Mold Release and Preparation
Prior to casting, a mold release agent is applied to ensure the easy removal of the final casted part from the mold. The mold is then preheated to a specific temperature to enhance material flow and reduce curing time.

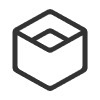
Step 4. Material Mixing and Vacuum Degassing
The chosen casting material, usually a two-part polyurethane (PU) resin, is mixed thoroughly to achieve a homogeneous consistency. The mixed material is then placed in a vacuum chamber to remove any air bubbles or voids that could affect the final part's quality.

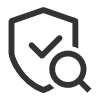
Step 5. Casting Process
The prepared mold is placed in a vacuum casting machine. The machine creates a vacuum within the chamber, which helps to draw the liquid resin into the mold, ensuring precise replication and minimal defects. The resin is poured into the mold under vacuum conditions, filling the cavities and replicating the desired geometry.

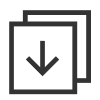
Step 6. Curing and Solidification
After the mold is filled, the casting is left undisturbed to cure and solidify. The curing time varies based on the resin type, thickness of the part, and ambient conditions. If necessary, heat or post-curing may be applied to accelerate the curing process

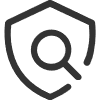
Step 7. Mold Opening and Part Extraction
Once the resin has solidified, the mold is opened, and the cast part is carefully removed. The mold can then be reused multiple times to produce additional parts.

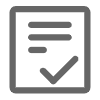
Step 8. Finishing and surface treatment
To achieve the desired aesthetics and functionality, the casted part may require finishing and surface treatment, such as trimming excess material, sanding, painting, or surface treatments.
See What Our Customers Say About Us
The feedback of customers has a greater impact than a company’s advertising. Take a look at what our satisfied customers have to say about how we met their needs.
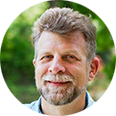
President and CEO
Wendy
I couldn’t be happier with the results of NOBLE Machining’s vacuum casting services, Their crew was attentive, responsive, and competent from the initial consultation to the final outcome. They understood our design needs and produced parts that were just what we needed. The items were of great quality, with tight tolerances and clear finishes. Their dedication to client satisfaction is palpable, and I would undoubtedly use their services again in the future.
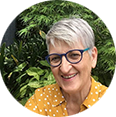
Automotive Designer
Ahmed
I worked with NOBLE on a vacuum casting project and was thrilled with the results. Their technical knowledge, advanced equipment, and attention to detail ensured flawless parts. Their project management and communication made the experience stress-free. Highly recommend their services for high-quality manufacturing solutions.
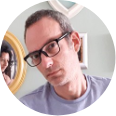
Aerospace Engineer
Vaibhav
NOBLE’s vacuum casting service was exceptional, with timely delivery and top-notch parts that met my precise requirements. Their attention to detail and focus on quality and accuracy are evident in all aspects of their work. Highly recommended for anyone seeking trustworthy vacuum casting services.
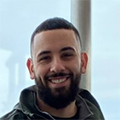
Mechanical Engineer
Mattew
I have received the vacuum casting parts that you created for me, and I had the opportunity to open the box and examine them today. They are truly impressive! I am extremely satisfied with the quality of your components. You have put in exceptional effort, and I appreciate it greatly. Thank you so much!
Advantages of Vacuum Casting
As a leading vacuum casting manufacturer in China, NOBLE provides low-cost manufacturing of high-quality plastic parts. Our vacuum casting services provide short-cycle solutions for creating high-quality prototypes and low-volume part production.
Vacuum casting, or urethane casting, is a technique that combines a silicone mold with a 3D printing master to create vacuum-cast parts with consistent performance and production-grade quality. The technology requires no costly up-front investment, allows for flexible, economical production, and process hardens thermoplastic polyurethane in silicone or epoxy molds. The result is a vacuum-cast part with the same shape as the original master model. The final dimensions of a vacuum cast part will depend on the master model, part geometry, and material chosen.
Vacuum Casting Applications
Because CNC machining can achieve high precision without changing the material structure with good manufacturing speed, it is becoming growing common as the range of machines, control systems, and tools for CNC machining continues to expand.NOBLE is dedicated to providing precision machining services for various industries and our precision CNC-crafted parts can be found in all areas of the industry, including.

Oil & Gas
Experts at NOBLE master the comprehensive knowledge of CNC machining for the oil field and gas industry paired with the assurance of high precision offered by top-notch CNC machines.
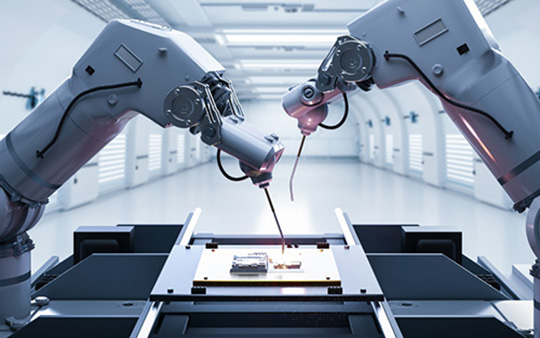
Automation Equipment
NOBLE Rapid Prototyping service allows you to quickly and easily create automated functional prototypes to test and optimize your design, select the right process, reduce costs, and shorten project cycles. On-demand services can produce automated parts with a high level of accuracy.
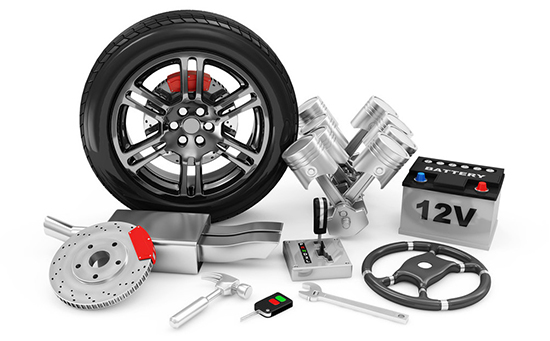
Automotive
Our low-volume manufacturing services is the ideal manufacturing solution for on demand automotive parts.
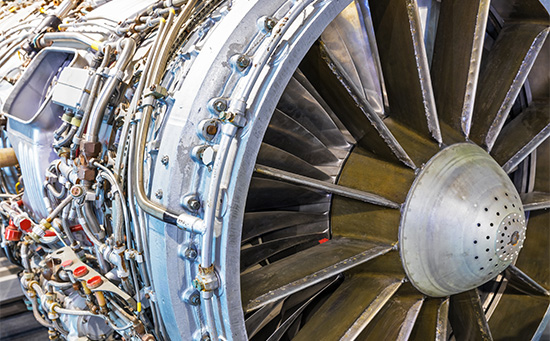
Aerospace
The durability and precision that our precison manufacturing services provide meets the sophisticated needs the different phases of the aerospace industry required.
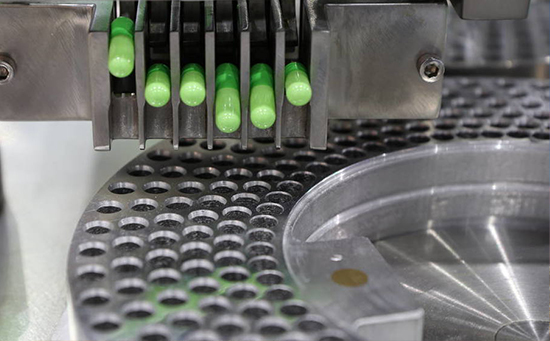
Medical Devices
Medical supplies manufacturers, tech startups, and research labs benefit significantly from the prototyping solutions we provide.
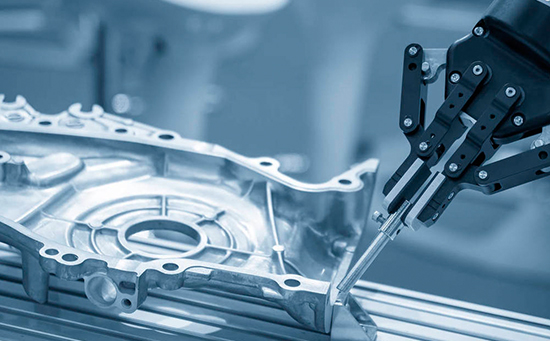
Robotics
Our industrial-grade robotics prototyping and parts manufacturing services aid in the continuous evolution of the robotics market.
If you are looking for a rapid prototyping manufacturer or a CNC machine shop to fabricate small, medium-volume, or mass-production products, NOBLE is an ideal choice.Our well-trained and experienced staff manufactures parts in line with drawings on modern CNC machines, with the highest accuracy and processing quality in all sizes.In addition, we provide professional design considerations for your CNC machining projects.
Want to get the most professional and fastest service for your CNC machining project? Upload your CAD files now and obtain a quote!
Vacuum Casting FAQs
Vacuum casting is a manufacturing process that involves creating replicas of a master pattern by pouring liquid resin into a silicone mold under vacuum conditions. It is commonly used for prototyping and low-volume production of complex parts.
Vacuum casting is compatible with a wide range of materials, including polyurethane (PU) resins. These resins come in various formulations, offering different mechanical properties, colors, and finishes to suit specific application requirements.
Vacuum casting is a manufacturing process used to create prototypes or small production runs of plastic parts. It involves creating a mold around a master pattern, pouring liquid resin into the mold, and using a vacuum to remove air and ensure complete resin filling. The resin is then cured, and the mold is separated to remove the solidified parts. Vacuum casting allows for high-quality replicas with detailed features and is cost-effective for low-volume production.
Vacuum casting provides a flexible, cost-effective, and efficient solution for creating prototypes, producing low volumes of parts, and achieving high-quality replicas with intricate details and fine finishes.
The lead time for vacuum casting can vary depending on several factors, including the complexity of the part, the number of parts required, the specific requirements of the project, and the capacity of the manufacturing facility. Generally, the lead time for vacuum casting can range from a few days to a few weeks.
It’s important to note that the cost-effectiveness of vacuum casting versus injection molding can vary depending on the specific project requirements. For high-volume production runs, injection molding becomes more cost-effective due to the amortization of tooling costs over a larger number of parts. It’s recommended to assess the specific needs of your project and consult with manufacturers or service providers to determine the most cost-effective manufacturing method.
Vacuum casting offers several advantages for prototyping, including quick turnaround times, cost-effectiveness, and the ability to produce functional prototypes that closely resemble the final product in terms of aesthetics and physical properties.