Sheet Metal Welding
Our Sheet Metal Welding Services
Providing custom sheet metal welding services that exceed customer expectations at competitive prices. From prototyping to sheet metal welding manufacturing, our experienced team and advanced production equipment ensure you receive sheet metal welding parts with high precision and stable performance. Get a quote in minutes and sheet metal welding parts in days!
- ISO 9001 & ISO13485 Certified Factory
- Advanced Equipment & Competitive Price
- 10+ Years of Sheet Metal Fabrication
- Compliant Sheet Metal Welding Standard
- Lead Time As Fast As 3 Days
- 24/7 Engineering Support

STEP | STP | STL | IGS | IGES | PRT | SLDPRT | SAT | X_T | IPT | CATPART | PDF
Max. file size: ≤20MB
- All uploads are secure and confidential.
Our Sheet Metal Welding Processes
NOBLE is equipped with state of the art sheet metal welding equipment and cutting-edge technology, allowing us to tackle the most challenging Sheet Metal Welding tasks with ease. Our team of highly skilled and experienced welders has an in-depth knowledge of various welding techniques and processes. Whether it’s complex metal fabrication, structural welding, or repairs, our experts bring unparalleled craftsmanship to every project.
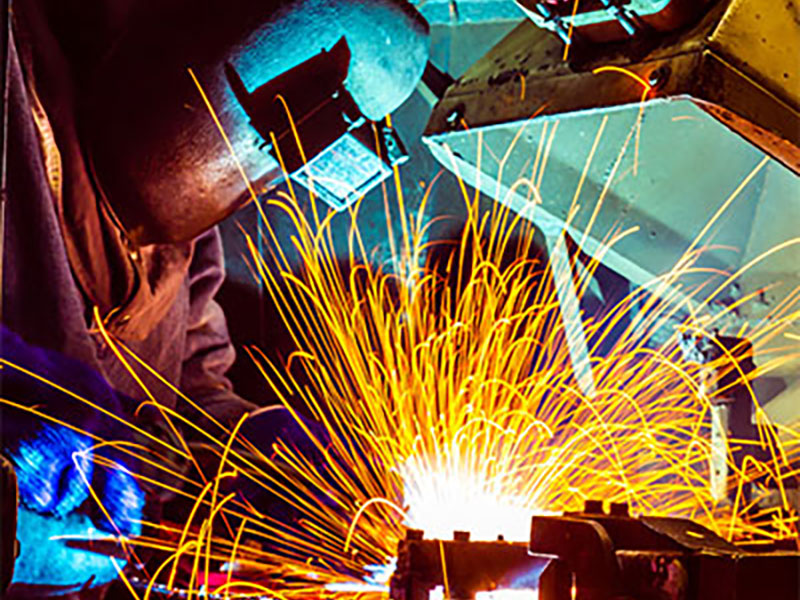
MIG welding, also known as GMAW (Gas Metal Arc Welding), is a well-liked welding technique that utilizes a welding gun to feed a continuous wire electrode. The weld is safeguarded from atmospheric pollutants by a shielding gas, which may be either inactive (e.g. argon) or active (e.g. carbon dioxide). GMAW is recognized for its flexibility, user friendliness, and ability to weld a variety of metals including steel, aluminum, and stainless steel.
- Precise Control of Arc Energy
- Competitive Price 30% Cost Save
- Fast Turnaround in 7 days
- Quick Turn MIG Welding Services
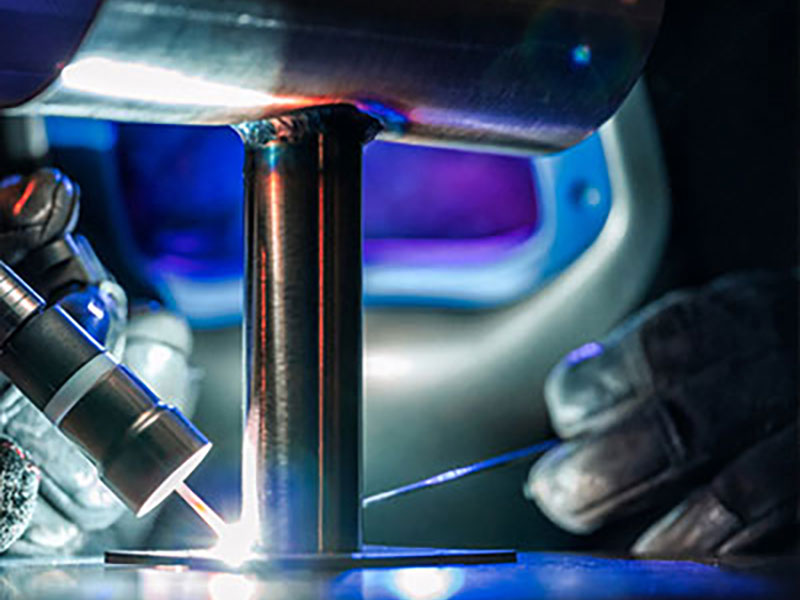
TIG (Tungsten Inert Gas) welding, also known as GTAW, is a versatile and precise welding technique. It involves the use of a non-consumable tungsten electrode to create an electric arc, which is shielded by an inert gas, typically argon. TIG welding is preferred for its exceptional control over the welding process, which results in high-quality welds on a variety of metals such as stainless steel, aluminum, copper, and titanium. It is a popular choice for applications that require top-notch weld quality and an aesthetically pleasing finish.
- Ultra-thin Plate Welding
- Quote Within 24 hours
- Fast Turnaround in 7 days
- Quick Turn TIG Welding Services
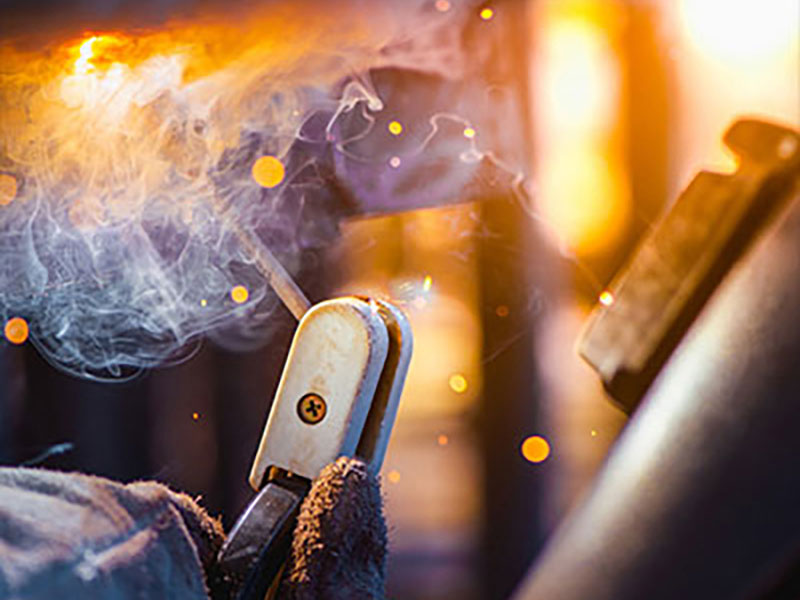
SMAW, also known as stick welding, is a popular welding process used widely. This method uses a consumable electrode coated with flux. An electric arc is created between the electrode and the workpiece, melting the electrode and creating a weld pool. The flux coating acts as a protective shield, preventing the weld from atmospheric contamination. SMAW is a versatile welding process and can be used for welding different metals such as steel, stainless steel, cast iron, and others.
- State-of-the-art Equipment
- Smooth Weld Surface
- Fast Turnaround in 7 days
- 1-to-1 Quote Analysis
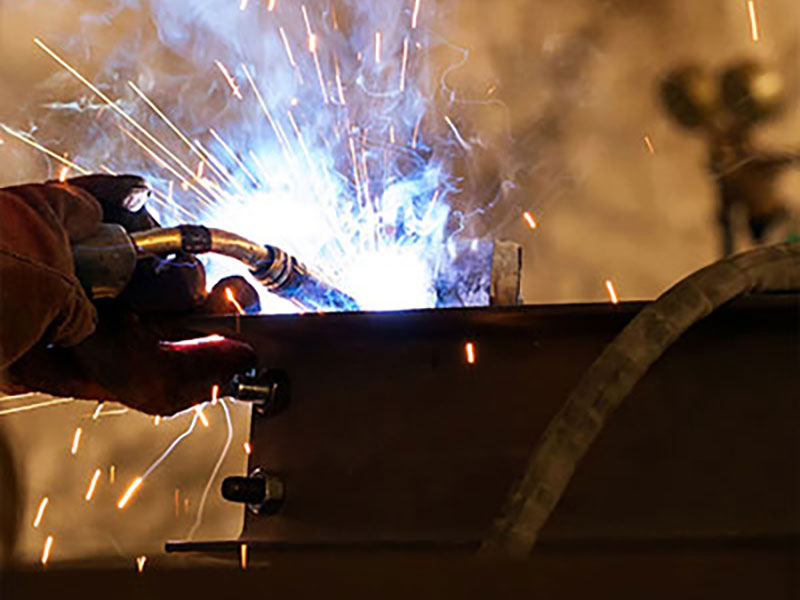
FCAW is a welding process that involves using a tubular wire electrode with flux inside. This flux creates a shielding gas, which means that an external shielding gas source is not required. It is known for its ability to deposit material at high rates and penetrate deeply, making it suitable for heavy-duty applications. FCAW is commonly used in construction, shipbuilding, and pipeline welding, particularly for thick materials and in outdoor or windy conditions.
- High Precision & Efficiency
- Competitive Price 30% Cost Save
- Fast Turnaround in 7 days
- Quick Turn FCAW Welding Services
Our Sheet Metal Welding Services Capabilities
Sheet Metal Prototyping to Production
NOBLE is your trusted one-stop custom manufacturing solution, from prototype design to manufacturing, through huge manufacturing resources, suitable technology, streamlined process, expert guidance, and perfect quality inspection process to turn your ideas into reality.
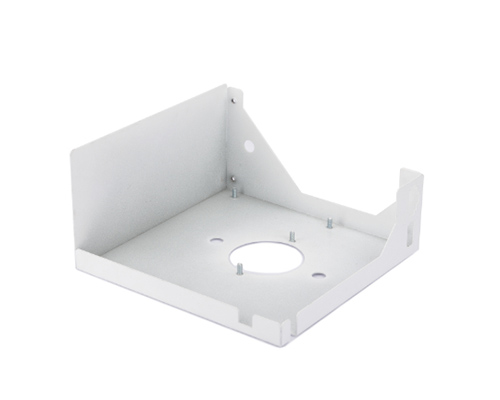
Sheet Metal Prototype Machining
At NOBLE, you can get an online sheet metal fabrication quote and free design analysis within hours, and have your sheet metal fabrication prototype completed within days.
- State-of-the-art Equipment
- 10+ Years of Sheet Metal Manufacturing
- Competitive & Affordable Price
- Quote Within 24 hours
- Free DFM Feedback
- Fast Turnaround in 7 days
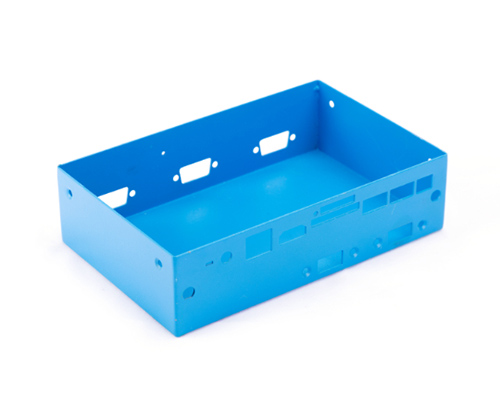
Rapid Sheet Metal Prototyping
With advanced production equipment and an experienced team of engineers, our sheet metal prototypes can be produced within a few days at a low unit cost, with strict tolerance control and a complete quality inspection process.
- Competitive & Affordable Price
- State-of-the-art Equipment
- 10+ Years of Low-Volume Manufacturing
- Fast Lead Time
- 30+ Countries shipped
- 100% Part Inspection
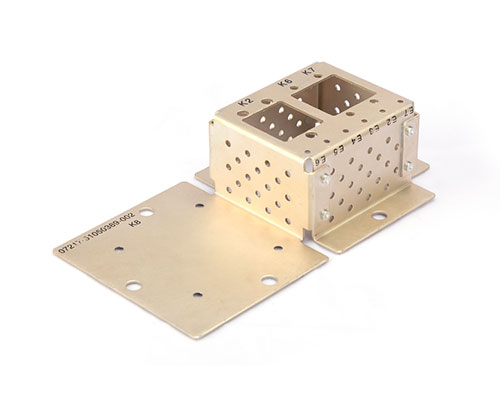
Batch Sheet Metal Production
NOBLE meets mass production needs through strict tolerance control, quality inspection, and a complete supply chain, and quickly delivers large quantities of low-cost, stable-performance sheet metal parts.
- 10+ Years of Medium&Mass Production
- Competitive & Affordable Price
- Large Supplier Network
- 100,0000+ Unique parts produced
- Guaranteed Consistent Quality
- Fast Turn-Around Production
Why Choose Us for Custom Sheet Metal Welding Services
NOBLE attaches great importance to customer satisfaction by using state of the art welding technology and an experienced team. Our sheet metal welding services are precise, efficient, cost-effective, and produce superior results. By using our sheet metal welding services, your business can be more successful.
Strong Sheet Metal Welding Capabilities
We offer TIG, MIG, spot welding, seam welding, laser welding, and other sheet metal fabrication services at competitive prices. With advanced sheet metal welding technology and an experienced team of engineers, we provide you with flexible material and surface finish options to meet your diverse sheet metal welding needs.
Competitive Pricing
Provide you with high-precision customized sheet metal welding services at competitive prices, from prototype design to sheet metal fabrication, and tailor-made sheet metal welding solutions for you to ensure you get excellent sheet metal welding parts. Our talented team can provide value-added solutions that exceed your budget.
Extensive Selections
We offer every possible material type, surface finish option, tolerance, and manufacturing process for your sheet metal welding. Depending on your custom sheet metal welding parts needs, we provide you with different quotes and manufacturing recommendations so that you can get a personalized approach and the most cost-effective solution.
Engineering Support
If you need engineering support, our team is available 24/7 to help. Our experienced sheet metal fabrication engineers can help you with part design, material selection, surface treatment options, and even delivery time recommendations. Rest assured, no matter where you are, we can meet your needs.
Work with Us in 4 Simple Steps Only
With many years of manufacturing experience, NOBLE offers the best solutions for all rapid prototyping and low-volume manufacturing needs. We streamline the innovation cycle into four simple but effective steps.



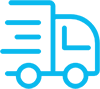
CNC Machining Tolerances and Standards
With precision CNC machining services, NOBLE is your ideal partner to create precision machined prototypes and parts. Our standard CNC machining tolerances for metals is ISO 2768-f and for plastics is ISO 2768-m. We can also achieve special tolerances as long as you indicate your requirements for your drawing.
Standards | CNC Milling | CNC Turning |
Maximum Part Size | 2000×1500×600 mm | 200×500 mm |
Minimum Part Size | 4×4 mm 0. 1×0. 1 in | 2×2 mm 0. 079×0. 079 in |
Minimum Feature Size | Φ 0. 50 mm Φ 0. 00197 in | Φ 0. 50 mm Φ 0. 00197 in. |
Standard Tolerances | Metals: ISO 2768-f Plastics: ISO 2768-m | Metals: ISO 2768-f Plastics: ISO 2768-m |
Hole Diameters | +/- 0. 025 mm +/- 0. 001 in. | +/- 0. 025 mm +/- 0. 001 in |
Linear Dimension | +/- 0. 025 mm +/- 0. 001 in | +/- 0. 025 mm +/- 0. 001 in. |
Edge Condition | Sharp corner will be removed in the form of a chamfer or radius. The size of the chamfer, or resulting radii, must be indicated on the drawing. | |
Shaft Diameters | +/- 0. 025 mm +/- 0. 001 in | +/- 0. 025 mm +/- 0. 001 in. |
Threads and Tapped Holes | Diameter: Φ 1. 5-5 mm, depth: 3×diameter Diameter: Φ 5 mm or more, depth: 4-6×diameter | Diameter: Φ 1. 5-5 mm, depth: 3×diameter Diameter: Φ 5 mm or more, depth: 4-6×diameter |
NOBLE can produce threads of any specification and size required by our customers. | ||
Text | Minimum width of 0. 5 mm, depth of 0. 1 mm | NOBLE can use laser marking to create standard text for CNC turned parts. |
Lead Time | 3 business days | 3 business days |
Materials for Sheet Metal Welding
There are various metallic materials that react differently to heat. They have different melting points, tensile strengths, and ductility. Before welding, the welder should understand the material’s characteristics and limitations to achieve optimal sheet metal welding results.
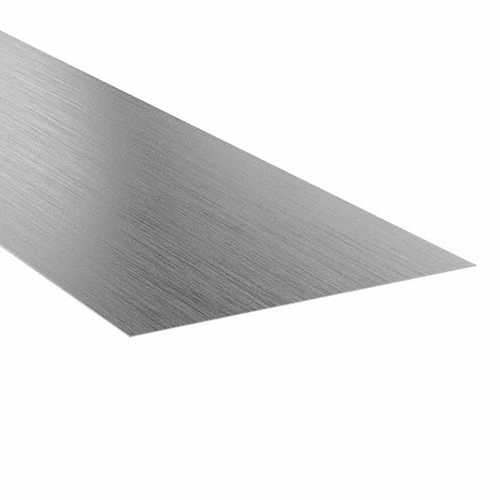
Carbon Steel
Many people choose to use carbon steel for welding because it is versatile, affordable, and easy to find. This type of steel is made up of iron and carbon, with small amounts of other elements. Carbon steel can be used in a variety of ways, such as for structural welding, fabrication, automotive, and machinery purposes.
Price: $
Lead Time: 3 days
Tolerances: ±0. 01mm
Max part size: 200 x 80 x 100 cm
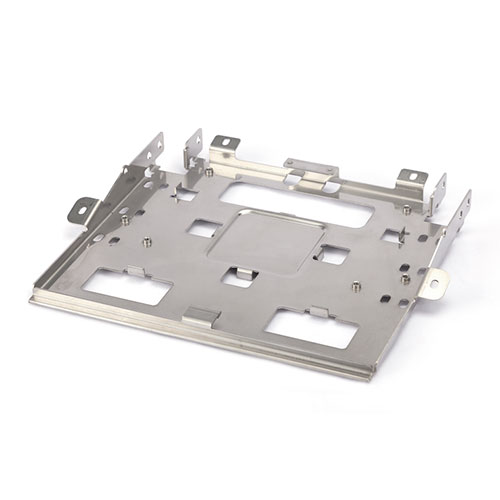
Stainless Steel
Stainless steel is composed of chromium, which gives it excellent heat resistance but also causes it to absorb heat. Therefore, when working with stainless steel, it’s important to work quickly and accurately to avoid warping or scratching the surface. Depending on the project and the level of precision needed, both MIG and TIG welding can be used with stainless steel.
Wall Thickness: 0. 75 mm
Lead Time: 3 days
Tolerances: ±0. 01mm
Max part size: 200 x 80 x 100 cm
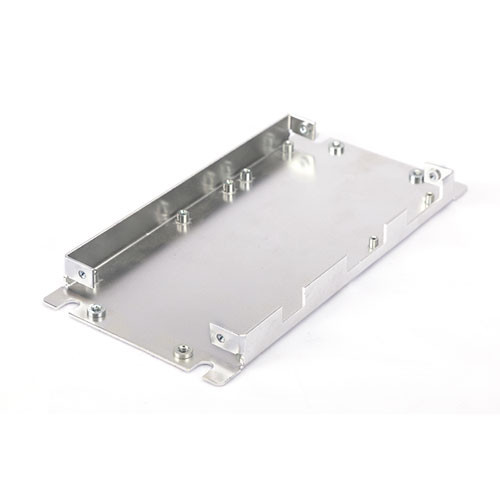
ALuminum
Aluminum is a lightweight metal known for its excellent strength to weight ratio, high conductivity, and corrosion resistance. It is widely used in industries such as aerospace, automotive, marine, and construction. Aluminum welding requires specific techniques and equipment due to its low melting point and high thermal conductivity.
Wall Thickness: 0. 75 mm
Lead Time: 3 days
Tolerances: ±0. 01mm
Max part size: 200 x 80 x 100 cm
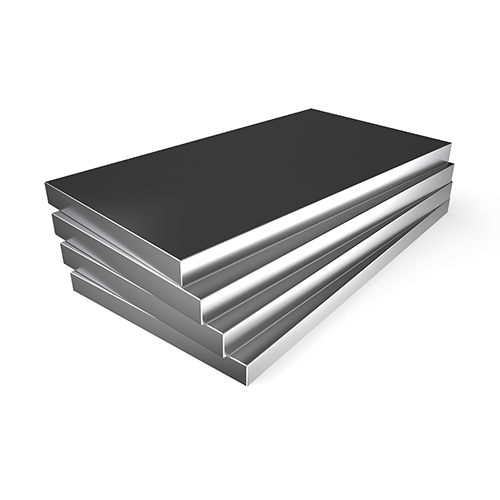
Titanium
Titanium is a type of metal that is known for being lightweight and extremely resistant to corrosion. Due to its exceptional strength, it is frequently utilized in industries such as aerospace, medical devices, and chemical processing. However, the process of welding titanium requires strict controls, specialized equipment, and an inert shielding atmosphere.
Wall Thickness: 0. 75 mm
Lead Time: 3 days
Tolerances: ±0. 01mm
Max part size: 200 x 80 x 100 cm
Surface Finishes for Sheet Metal Welding Parts
Surface treatments from NOBLE can assist in improving the surface quality of your items. Surface treatments on custom items are designed to improve their look, surface hardness and roughness, chemical and corrosion resistance, and other qualities. They also aid in the concealment of any obvious tool marks from regions cut with live tooling. Here are some of your greatest options.
Anodizing
Anodizing improves corrosion resistance, enhancing wear resistance and hardness, and protecting the metal surface. Widely used in mechanical parts, aircraft, and automobile parts, precision instruments, etc.
Materials: Aluminum
Color: Clear, black, grey, red, blue, gold.
Texture: Smooth, matte finish
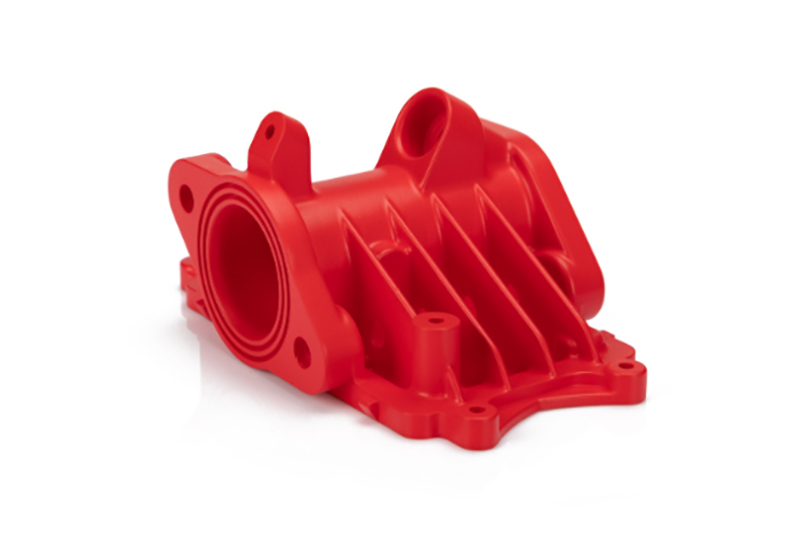
Powder Coating
Powder coating is a type of coating that is applied as a free-flowing, dry powder. Unlike conventional liquid paint which is delivered via an evaporating solvent, powder coating is typically applied electrostatically and then cured under heat or with ultraviolet light.
Materials: Aluminum, Stainless Steel, Steel
Color: Black, any RAL code or Pantone number
Texture: Gloss or semi-gloss
Electroplating
Electroplating can be functional, decorative or corrosion-related. Many industries use the process, including the automotive sector, in which chrome-plating of steel automobile parts is common.
Materials: Aluminum, steel, Stainless Steel
Color: N/A
Texture: Smooth, Glossy finish
Sand Blasting
Sand blasting results in parts with a smooth surface with a matte texture. Used mainly for visual applications and can be followed by other surface treatments.
Materials: ABS, Aluminum, Brass
Color: N/A
Texture: Matte
Polishing
Polishing is the process of creating a smooth and shiny surface, either through physical rubbing of the part or by chemical interference. The process produces a surface with significant specular reflection, but in some materials is able to reduce diffuse reflection.
Materials: Aluminum, Brass, Stainless Steel, Steel
Color: N/A
Texture: Glossy
Brushing
Brushing is a surface treatment process in which abrasive belts are used to draw traces on the surface of a material, usually for aesthetic purposes.
Materials: ABS, Aluminum, Brass, Stainless Steel, Steel
Color: N/A
Texture: Satin
Custom Sheet Metal Welding Parts Display
Please browse our extensive gallery showcasing the precision sheet metal weldments created by us for our esteemed clients.
See What Our Customers Say About Us
NOBLE has been engaged in Sheet metal fabrication services for over ten years and has served many overseas customers. Customers’ words are more substantively representative than the company’s statement–see the objective evaluation of our satisfied customers.
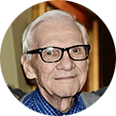
Mark Alford
Vice President
From the instant and accurate quotation to the production process to the timely delivery of parts, NOBLE responded to our demands with complete professionalism.They handled every aspect of this CNC machining project quickly and cost-effectively.We will surely work with them again in the future.
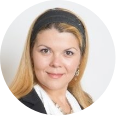
Piscary Herskovic
Product Designer
NOBLE has been our quality supplier of CNC machined parts.Fast delivery is very important for our business, and NOBLE always offers short lead time and competitive pricing.Andy responds fast to all our emails and questions.This has improved our working relationship, and we continue to value this partnership.
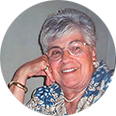
Hari Mackenzie
Engineer
We asked NOBLE to fabricate parts for a critical supplier demo, and you came through with a short lead time.Your work is always high quality, and we are grateful for your precision in machining components. The help in checking our designs and material selection has also saved our company from making expensive errors.We look forward to doing future projects with you guys.
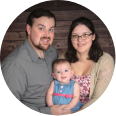
Stefan Hohmann
Product Manager
My experience with NOBLE has been nothing but exceptional. From the start, the communication has been accurate and fast. Specificities of the design that may meet production difficulties are promptly pointed out with suggested solutions. The price of CNC machined parts is competitive. The QC of the final product is also excellent. There is no doubt that I will go back again.
Sheet Metal Welding of Applications
Metal welding is a crucial aspect of parts manufacturing in various industries such as automotive, aerospace, electronics, appliances, telecommunications, and medical equipment. NOBLE is dedicated to offering innovative manufacturing solutions to meet the diverse needs of our clients. Our top priority is to provide high-quality parts at competitive prices to customers across multiple sectors.

Oil & Gas
The precise and reliable nature of sheet metal cutting makes it a valuable technique in the oil and gas industry for fabricating components and structures that meet stringent requirements for strength, durability, and safety.
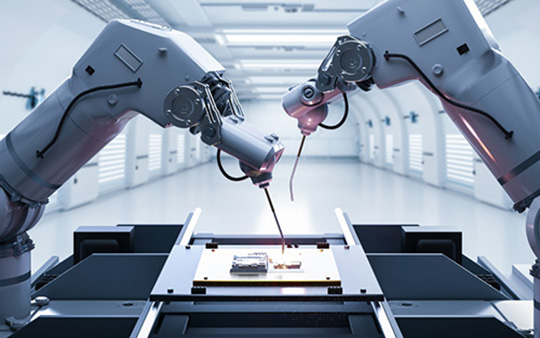
Automation Equipment
NOBLE Rapid Prototyping service allows you to quickly and easily create automated functional prototypes to test and optimize your design, select the right process, reduce costs, and shorten project cycles. On-demand services can produce automated parts with a high level of accuracy.
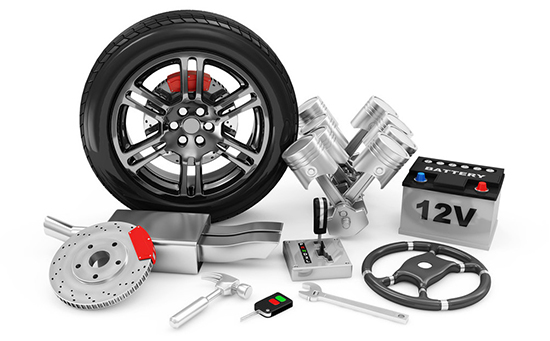
Automotive
Sheet metal cutting is a precise and flexible method used in tool and die applications to produce components and accessories that meet the rigorous demands of various industries such as automotive, aerospace, and manufacturing.
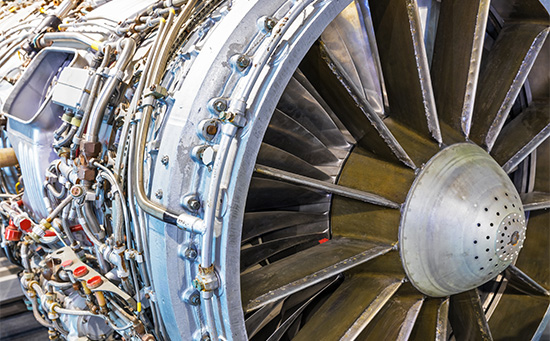
Aerospace
Precision and close tolerances are necessary for aerospace components. Some lightweight, space-ready component parts like bespoke interface panels, airfoils, and sensor enclosures could be machined by using custom metal cutting services.
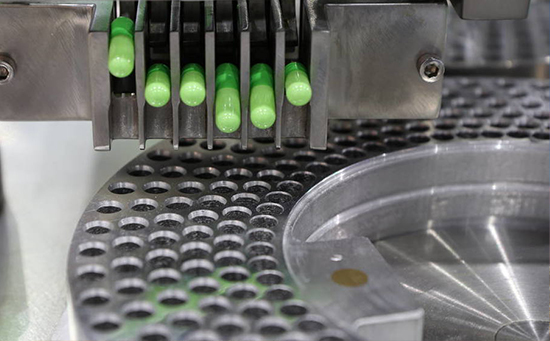
Medical Devices
The process of metal cutting is readily available and offers a reliable way to produce long-lasting medical components that meet high standards of accuracy and quality. It can be utilized in the creation of scalpels, surgical instruments, and other essential medical equipment.
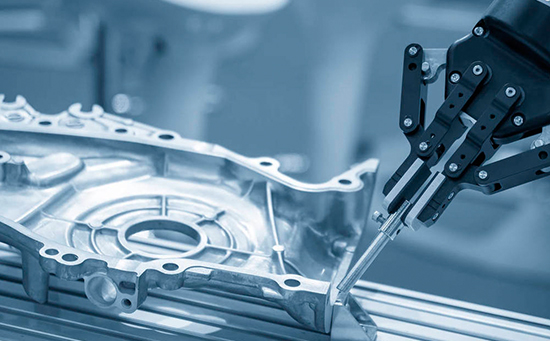
Robotics
Sheet metal cutting services are indispensable for precise, strong, and customizable robotics applications. They can create bespoke components that seamlessly integrate with the robot's design and function.
If you are looking for a rapid prototyping manufacturer or a CNC machine shop to fabricate small, medium-volume, or mass-production products, NOBLE is an ideal choice.Our well-trained and experienced staff manufactures parts in line with drawings on modern CNC machines, with the highest accuracy and processing quality in all sizes.In addition, we provide professional design considerations for your CNC machining projects.
Want to get the most professional and fastest service for your CNC machining project? Upload your CAD files now and obtain a quote!
Sheet Metal Welding of FAQs
Sheet metal welding is the manufacturing process of melting and fusing metal or thermoplastics to create strong and permanent connections. Heat is used to melt the materials, and a filler material is added to assist the bonding process. The solidified bond is durable and unbroken.
Sheet metal welding is based on the controlled heating, melting, and fusion of materials, and the use of filler materials (if necessary), to create a strong and durable bond between the parts being joined. Material type, joint design, expected strength, and special application requirements all influence the parameters of the sheet metal welding process, equipment, and use.
Sheet metal welding plays a vital role in multiple industries, including joining and fabricating metal components, infrastructure construction, product manufacturing, maintenance and repair work, and even artistic creation. It provides versatility in material applications and has a significant economic impact. The process of creating a strong and reliable connection between materials makes welding an essential process.
Arc welding, gas welding, and resistance welding are the three main types of sheet metal welding, covering a variety of technologies and processes, each with its own advantages and applications. The choice of sheet metal welding method depends on a variety of factors, such as the materials being joined, the strength and quality of the sheet metal weld required, project requirements, and the skill and experience of the welder.
TIG welding is generally considered the strongest form of sheet metal welding because it generates intense heat and has a long cooling rate, resulting in high tensile strength and ductility. MIG is also a strong contender for the strongest form of welding because it produces a strong joint.
Learning Tungsten Inert Gas Welding (TIG) is widely considered the most challenging sheet metal welding process. This is due to the complexity of the technique, which requires more practice and concentration to master than other simpler methods of sheet metal welding. However, TIG sheet metal welding produces the strongest, most durable welds in the industry.
Acetylene is the most suitable fuel gas because of its ideal flame characteristics, including high temperatures and high propagation rates. While other gases such as propane, propylene, and natural gas are not sufficient for welding due to their low heat input, they still have uses in cutting, torch brazing, and welding.
There are several types of welding commonly used for sheet metal fabrication. Here are some of the most common sheet metal welding types:
TIG Welding (Gas Tungsten Arc Welding): MIG weldings a popular welding method that uses a consumable wire electrode and a shielding gas to protect the weld pool. It is relatively fast and suitable for both thin and thick sheet metal applications. MIG welding offers good productivity and can be easily automated.
Spot Welding: Spot welding is a resistance welding process that uses electrodes to apply pressure and heat to join two metal sheets together. It is commonly used in the automotive industry for joining sheet metal components. Spot welding is quick and efficient, producing localized welds without the need for additional filler material.
Seam Welding: Seam welding is a continuous welding process used to create long, leak-proof welds along the length of overlapping metal sheets. It is commonly used for joining sheet metal in applications such as tanks, pipes, and automotive body panels. Seam welding can be performed using TIG or MIG welding processes.
Laser Welding: Laser welding uses a high-energy laser beam to create a weld by melting and fusing the metal surfaces. It offers precise control and is suitable for both thin and thick sheet metal. Laser welding produces narrow and deep welds with minimal heat-affected zones.
Resistance Spot Projection Welding: Resistance spot projection welding is a variation of spot welding that uses specially designed electrodes to create a weld projection on one of the metal sheets. The projection allows for accurate alignment and improved joint strength in certain applications.