Quality Assurance
Speed up Your Project Without Sacrificing Quality
Placing product quality at the forefront of our manufacturing process, we integrate quality control in every step to ensure superior prototypes and parts. We identify critical quality criteria in each project and use them as benchmarks to measure the performance of the final products.
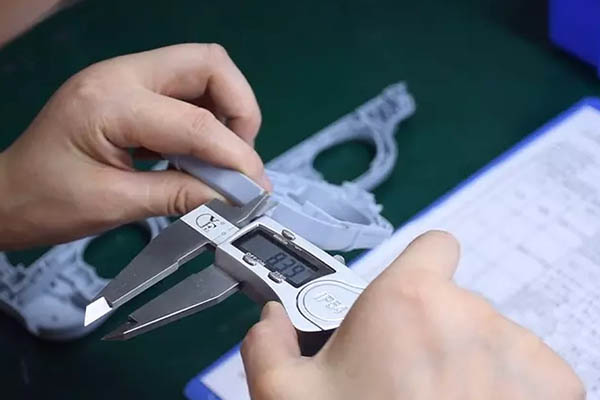
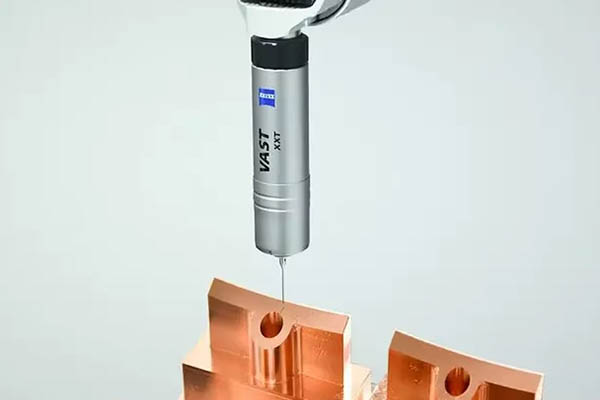
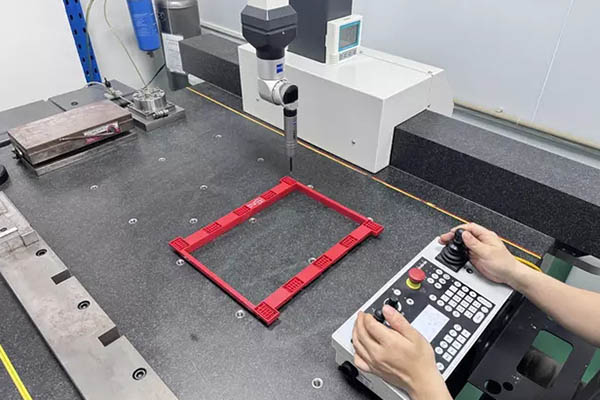
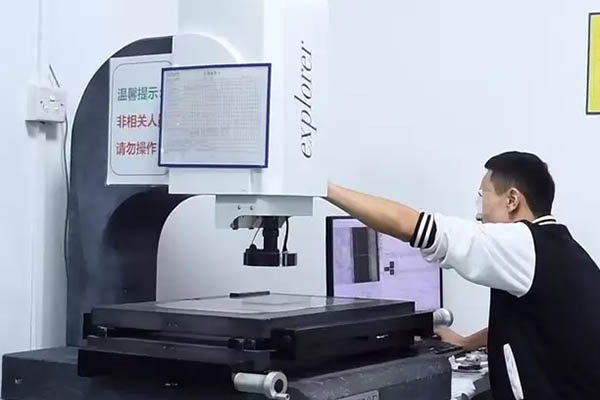
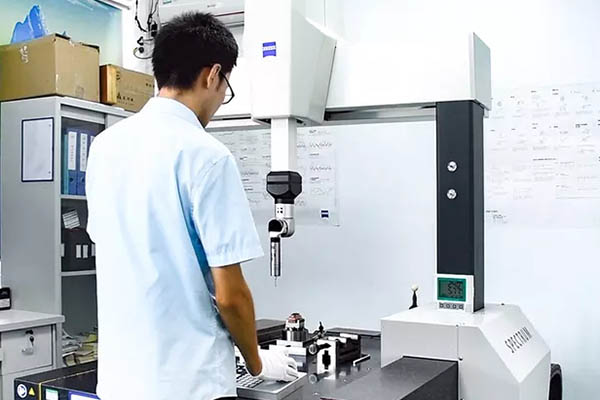
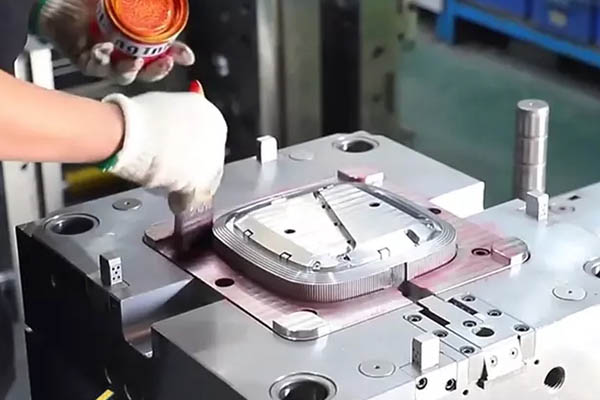
Speed up Your Project Without Sacrificing Quality
See how NOBLE maintains the highest quality standards in our production process, from material selection to final inspection.
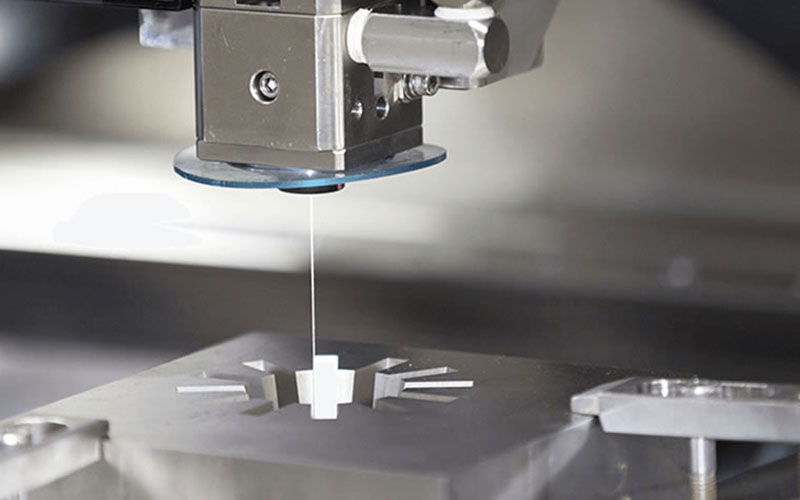
We carefully select the suppliers that we work with, ensuring they have the materials we need available and are of top quality.

Materials that arrive at our facility go through a series of tests, filtering top-grade materials from those with poor quality.
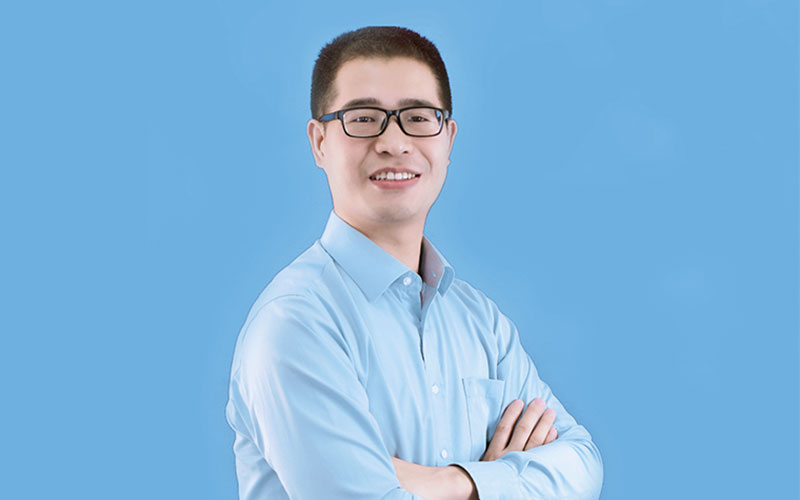
Rich experience in project management and order are controlling, mastered comprehensive knowledge and skills has a clear logical mind and good at time management and overall arrangement, maintains efficient operation by actively optimizing business processes, to offer good service for the customers. Excellent decision-making, coordination, planning, and managing skills.
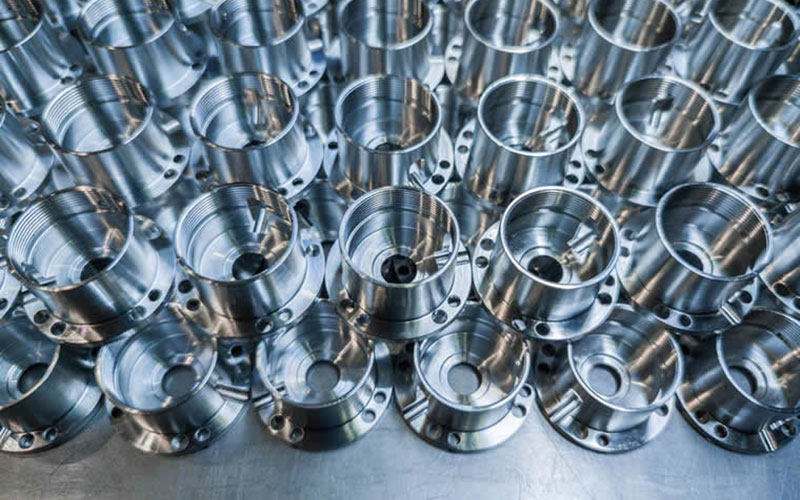
We practice a lean manufacturing workflow that adheres to ISO-2768-m and ISO-2768-c standards for tight tolerances.
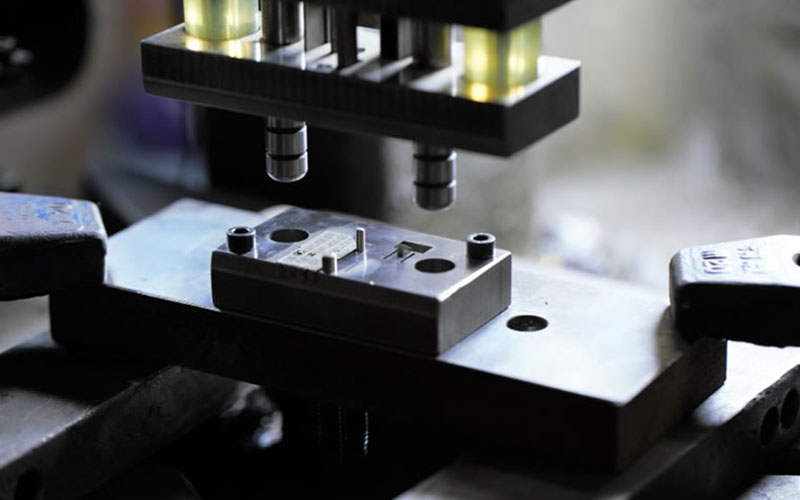
Our QC employees conduct a series of inspections, from material inspection, processing inspection, and finished product inspection.
Quality Control Process
Learn the most stringent inspection methods we apply over the course of the entire manufacturing process.
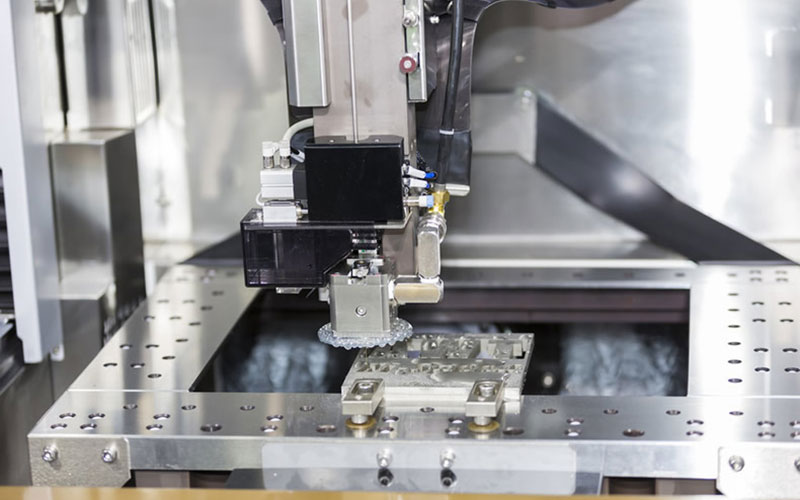
Before the production stage begins, our engineering team performs a technical assessment on your parts design. This includes an assessment on important factors such as material, surface finish, structure, process, and other details of your 3D and 2D drawings.
On our customer’s request, we provide a certification of the material we used for making your parts. The report comes from the raw material manufacturer and usually includes: material heat number, material grade, material dimensions, mechanical properties, chemical analysis, etc.
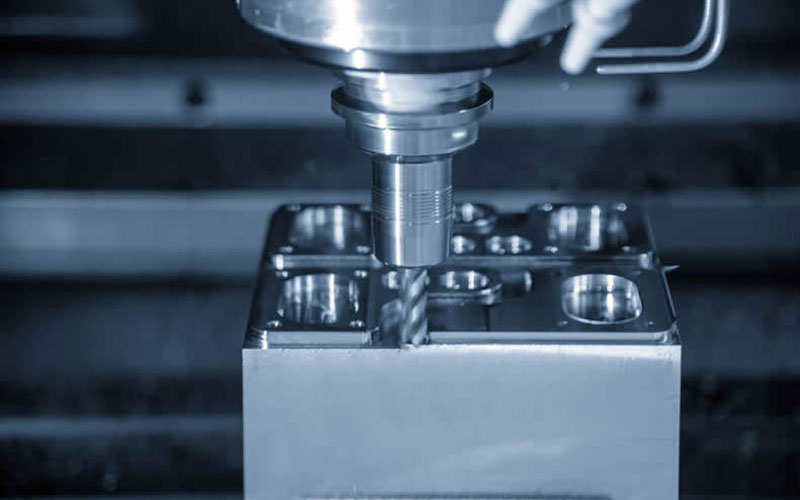
In precision machining, it is important that materials being worked on are always at the right position. With an on-site inspection system, positions are examined automatically, and adjustments are made accordingly. Using on-site inspection system further helps avoid issues at the early stage, saving cost and time.
At NOBLE, we strictly obey the ISO9001:2015 requirements. The quality control staff conducts routine inspections for all parts that are being produced every 2 hours. This further prevents risks from happening.
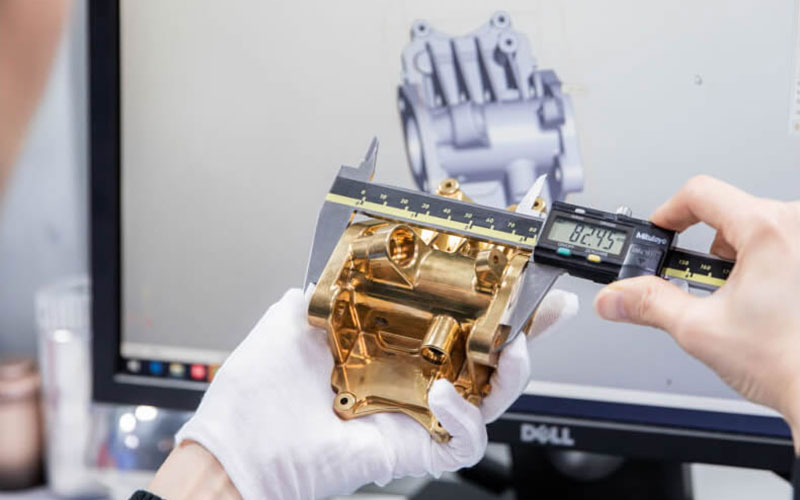
For all orders, we provide full dimensional inspection report on request. This report will include the following: quantity of parts, critical dimensions, threads and tolerances, thicknesses and depths, part appearance, etc.
Ensuring that the parts we manufacture are of the highest quality is important. We know about the unpredictability of logistics. Therefore, we make sure we lower the risk to the parts during our packaging process. Four layers of protection: 1. wrapping paper 2. EPE 3. foam 4. paper/wooden box are applied during the packaging process, ensuring that we deliver the most high-quality and beautiful parts to you.
State-of-the-art Facilities
To facilitate our strict quality control protocols, our production facility has dedicated workshops for meticulous inspection and state-of-the-art equipment.
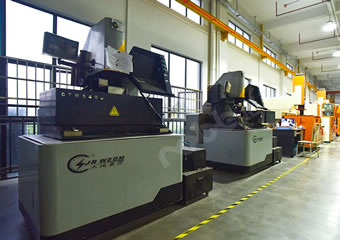
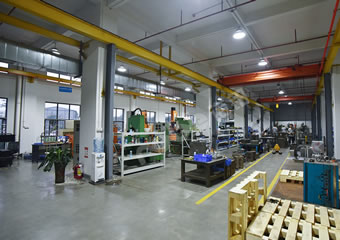
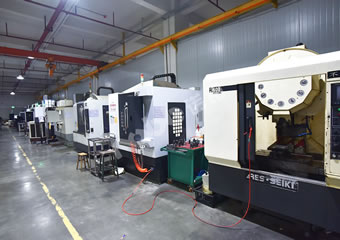
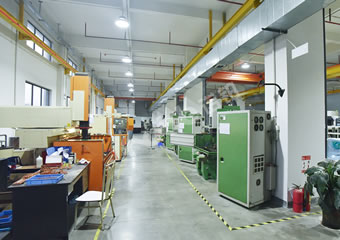
Quality Reports on Your Request
Giving you added confidence in the prototypes and parts we manufacture for your brand, we can provide detailed quality reports showing material quality and product performance. These reports can come from either our in-house auditors or from third-party laboratories.
For each order we receive, we can secure a list of quality reports per your request.
- Inspection report
- Full dimensional report
- Material test report
As an established manufacturer of on-demand products, we have a library of certifications from reputable organizations.
- ISO 9001:2015
- ISO 13485:2016
- ROHS
- REACH
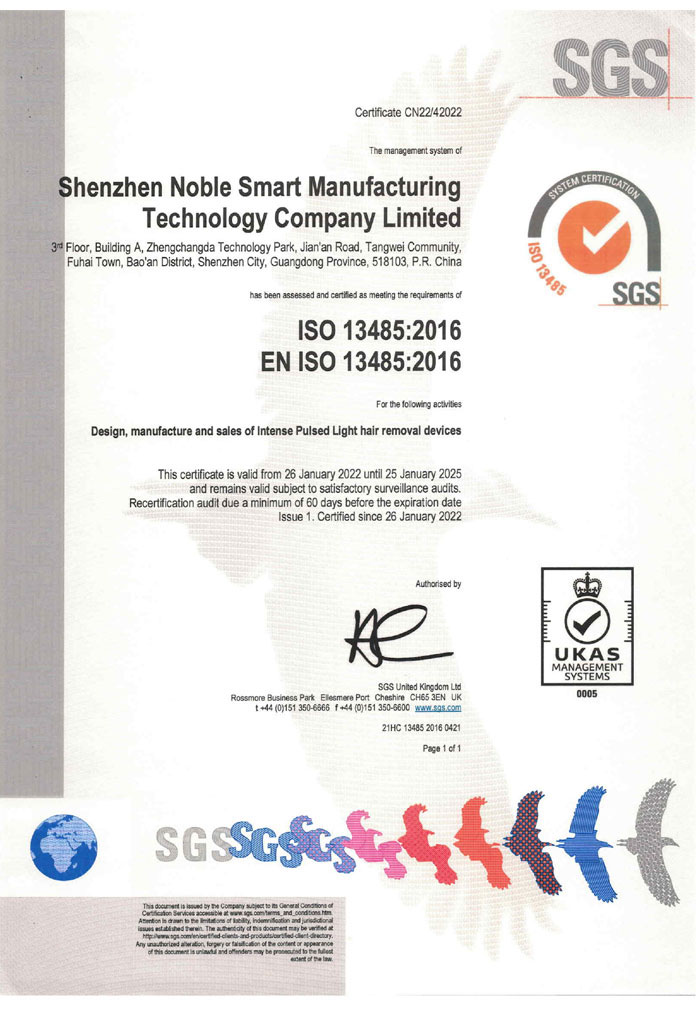
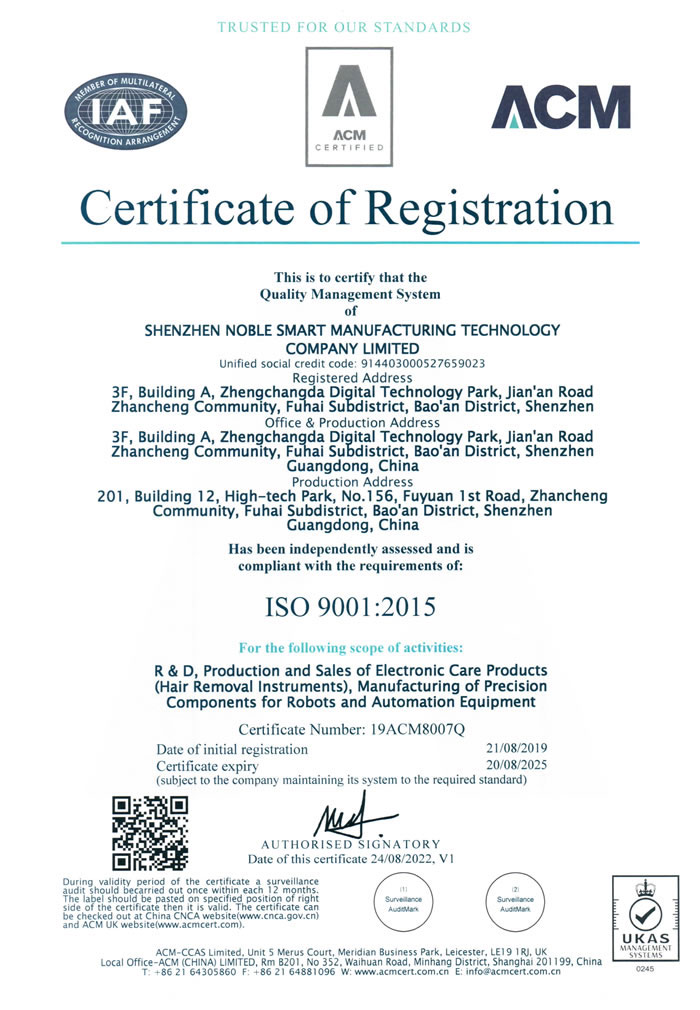
Resolving Quality Issues Without Hesitation
NOBLE aims to deliver exceptional prototypes and parts that fulfill your specific requirements. In the event that your order fails to meet your specifications, we can process a rework or a refund. Feel free to contact our experts if you come across any quality issues within 1 month after receiving your goods. Let us know of the issue within five business days from receipt, and we’ll address them within 1 to 3 business days.
After advising us of the concern, we review the design and samples to check for inconsistencies. We then fix the complaints and send replacements immediately.
- Unacceptable processing defects
- Fail to meet tolerance requirement
- Incorrect material / finish
Refunds are quickly processed upon confirmation of product issues, and return is processed.
- The part is not machinable
- The customer does not agree to rework
- Other reasons